Non-Destructive Robotic Disassembly of EV Batteries
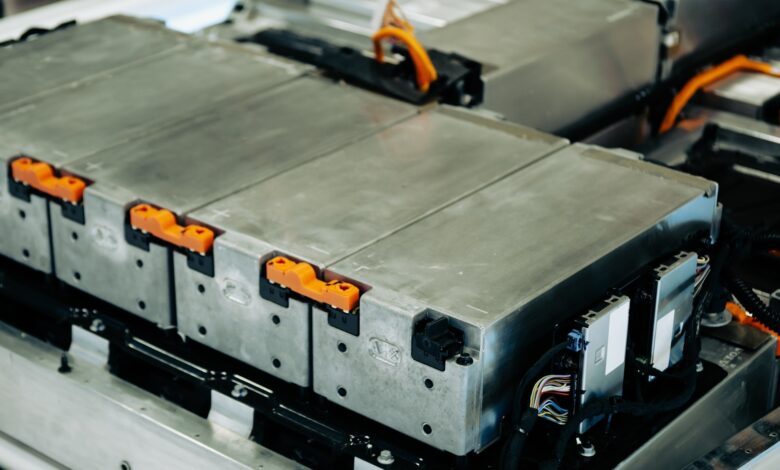
In a recent article published in the journal Automation, researchers from the UK presented a robotic platform for automating the non-destructive disassembly of a plug-in hybrid electric vehicle (EV) battery pack into modules.
They described the design and implementation of the platform, which uses four industrial robots equipped with different end-effectors and sensors to perform various tasks, such as unscrewing, localizing, and handling components. The research also evaluated the platform’s performance in terms of accuracy, robustness, and efficiency and identified some challenges and future directions for the robotic disassembly of EV batteries.
Background
EV batteries (EVBs) are an essential component of EVs that are expected to reduce greenhouse gas emissions and fossil fuel dependence. However, they also pose significant environmental and economic challenges when they reach their end-of-life (EoL), as they contain toxic and valuable materials that must be accurately processed. Recycling, repurposing, and remanufacturing are some of the possible EoL processing strategies for EVBs, but they all require an efficient and reliable disassembly process to separate the battery pack into modules or cells.
Manual disassembly of EVBs is not only time-consuming and labor-intensive but also hazardous and inconsistent due to risks such as short-circuiting, electroshocking, and electrolyte leakage. Robotic disassembly of EVBs offers a promising solution to enhance the safety, quality, and productivity of EoL processing. However, robotic disassembly presents its own challenges, as robots must navigate uncertainties, variations, and complexities inherent in EoL products and disassembly operations.
About the Research
In this study, the authors proposed a robotic disassembly/dismantling platform designed for non-destructive operations targeting the extraction of all seven battery modules from a plug-in hybrid EV battery pack with prismatic cells. Non-destructive operations involve tasks that preserve the original structure and function of components, including unscrewing, unfastening, and lifting.
This approach is essential for maintaining the value and functionality of components for potential recycling, repurposing, or remanufacturing purposes. The study aimed to demonstrate the concept and feasibility of autonomous disassembly of an EVB pack using robots while examining the critical operations and challenges involved in the process.
The platform consisted of four lightweight industrial robotic arms, each equipped with various end-effectors and sensors, including grippers, nutrunners, cameras, and force/torque sensors. Additionally, it incorporated a vacuum gripper, a tool-changing system, and an adapter-changing system to enhance versatility and adaptability. Control of the robotic arms was managed by an external personal computer (PC) that coordinated the workflow of each robot through communication using the transmission control protocol/internet protocol (TCP/IP).
Furthermore, the study described the disassembly sequence, which was divided into four distinct stages: top cover removal, circuit breaking, junction box removal, and battery module removal. Critical operations performed by the platform, such as unscrewing, localizing, and handling fasteners and components, was also demonstrated.
The authors also highlighted the design and implementation of the unscrewing system, which is responsible for all unscrewing operations in the disassembly process. The unscrewing system integrated a vision-based localization method, a force/torque sensor, an electric magnet, and a nutrunner adapter-changing method to achieve the following capabilities:
- Unscrewing and handling threaded fasteners
- Changing the nutrunner adapters for different situations
- Localizing the fasteners under positional uncertainty
- Addressing situations in which unfastened screws are jammed in the holes
The performance of the vision-based localization method was evaluated in terms of robustness against positional errors, which are common sources of failure in robotic disassembly. The authors compared three methods of initializing the unscrewing operation: without introducing any additional positional error, by introducing a random positional error without using the proposed method, and by introducing a random positional error and using the proposed method.
Research Findings
The outcomes showed that the newly developed method achieved the same success rate as the one without any additional positional error, proving the effectiveness of the method. The authors demonstrated the whole disassembly process of the battery pack, which involves 82 unscrewing operations and seven attempts to change the nutrunner adapters. They highlighted that their platform completed all the operations and extracted all seven battery modules from the pack.
Moreover, the study compared the operation time between the human operators and the robot platform and denoted that the human operators were faster than the robot platform. However, the research also points out that the robot platform has significant advantages from health, safety, and scalability perspectives and that the operation time can be further improved by optimizing the speed and efficiency of the platform.
The paper discussed the potential applications of the proposed platform for EV battery processing, emphasizing its role in supporting the recycling, repurposing, and remanufacturing of EVBs. It highlighted the platform’s capability to separate battery packs into modules without causing damage and to inspect and diagnose their condition and performance. Additionally, the authors suggested integrating the platform with other systems to create a complete EoL processing line for EVBs. The platform enables sustainable recycling by facilitating the separation and recovery of valuable materials and hierarchical repurposing by inspecting and replacing modules or cells based on their condition and quality. Moreover, it supports the remanufacturing of EV batteries by preserving functionality and value.
Conclusion
In summary, the platform demonstrated effectiveness and efficiency in automating hybrid EVB pack disassembly, offering potential benefits for battery recycling while preserving component integrity and functionality. The researchers acknowledged limitations and challenges in the disassembly process, such as tasks like removing cable ties, disconnecting cable harnesses, and separating coolant pads. These tasks require additional robotic disassembly tools and methods. Moving forward, the paper proposed several directions for future work, including implementing tool changer systems, reconfiguring the disassembly sequence, and enhancing the robots’ manipulation skills.
Journal Reference
Qu, M.; Pham, D.T.; Altumi, F.; Gbadebo, A.; Hartono, N.; Jiang, K.; Kerin, M.; Lan, F.; Micheli, M.; Xu, S.; et al. Robotic Disassembly Platform for Disassembly of a Plug-In Hybrid EV Battery: A Case Study. Automation 2024, 5, 50-67. https://doi.org/10.3390/automation5020005, https://www.mdpi.com/2673-4052/5/2/5