Why the future of manufacturing is human and robotic
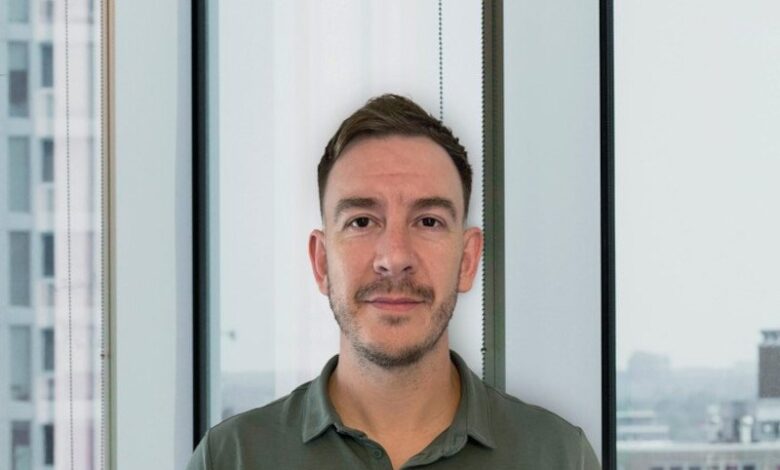
Cybersecurity manager Marc Wren argues that the latest movement in manufacturing aims to leverage the immense power of machines while also recognising the unique abilities that people bring to the table.
Industry 4.0, popularised by Klaus Schwab of the World Economic Forum in 2016, aimed to eliminate human involvement in manufacturing by accelerating automation. However, from 2020 onward, there has been a move towards humans and machines working in tandem, dubbed Industry 5.0.
While Industry 4.0 offers cost-saving benefits by automating processes, recent mishaps demonstrate the indispensable role of humans, and not just in manufacturing. For example, the self-driving car company Cruise had its licence suspended in San Francisco after a robotaxi dragged a pedestrian down the street.
To achieve greater efficiency, foster a culture of innovation and maintain a strong ethical reputation that avoids missteps similar to those encountered by Cruise, businesses are now adapting strategies that harness the unique strengths of both humans and more capable machines.
Despite some challenges, Industry 5.0 holds the promise of a brighter future, where humans and machines reshape the manufacturing sector for the better.
Robots as your new coworkers
At its core, Industry 5.0 recognises the irreplaceable value that people bring to the working world. While machines excel at tasks requiring repetition, speed, data ingestion and unwavering accuracy, humans possess a unique set of cognitive abilities that cannot be replicated by artificial intelligence – at least not yet.
From creativity and problem-solving skills to emotional intelligence and adaptive reasoning, the human mind remains an unparalleled asset in any industry. This collaboration will certainly change the game, as weaknesses from one side of the equation are eliminated by the strengths of the other.
For workers, the transition to Industry 5.0 represents an opportunity to leverage uniquely human abilities while upskilling to become more effective in the modern workplace. Rather than being replaced by automation, employees can become valued partners in the manufacturing process to drive continuous improvement and innovation.
Picture a transformed assembly line, where a line worker is equipped with a smart device for real-time data and instructions, collaborating with a robot to handle the heavy lifting and precise placement of components. Workers will also monitor the performance of automated systems, acting as guardians to identify and address any potential issues. Their critical-thinking and problem-solving skills will be crucial, and companies can further empower them by normalising training in these areas. Workers will need to adapt to unforeseen situations beyond the scope of their current automation, making computational thinking and basic coding skills another valuable area for normalised training.
This is likely to open doors for professional development, as companies invest in training and reskilling programmes in line with the necessary skills required to thrive in this era. For example, data analysis skills could become a standard part of onboarding for all new employees, regardless of their specific roles. This would equip them with the ability to understand and utilise data in their daily tasks, fostering a data-driven culture within the company.
Now is the time to change
Leading companies across various sectors are already embracing Industry 5.0. For instance, Ford Motor company has deployed ‘co-bots’ that work alongside human employees to handle physically demanding tasks while freeing up workers to focus on more cognitive-intense activities. This approach lays the foundations for the factories of the future – blending human expertise with technological advancements.
If workers are left behind and are unable to adapt to this paradigm, it could lead to significant societal challenges, including job losses, economic disparities and a widening skills gap that could hinder innovation.
As businesses adapt, a crucial aspect to consider is preparing the workforce for the changes ahead. As previously mentioned, comprehensive training and reskilling is essential. However, beyond technical know-how, fostering a culture of continuous learning and adaptation is equally important – being open to adapting mindsets is key. Businesses must prioritise creating an environment that encourages lifelong learning and personal growth.
Embracing the future of manufacturing
Undoubtedly, the transition to Industry 5.0 is not without its challenges and considerations. Concerns over job displacements and redundancies must be addressed, perhaps through vocational training. However, the point is not that machines will steal workers’ jobs, rather, workers who fail to understand the value and function of these machines may find themselves left behind.
Also, businesses mustn’t overlook the cybersecurity risks associated with the increased integration of connected systems and data exchange. Strong security measures and protocols must be implemented to safeguard sensitive information and protect against these threats.
For example, implementing multifactor authentication and network segmentation can help mitigate the risk of unauthorised access to critical systems and data. Businesses may also want to consider investing into specific cybersecurity awareness training for employees to educate them on common threats and best practices for protecting sensitive information.
Despite these challenges, the future promised by Industry 5.0 is one where humans and machines become seamless partners. Imagine factories where people’s strengths are supported by artificial intelligence, enabling them to tackle complex problems and unlock game-changing solutions. Workplaces where creativity and critical thinking are valued as highly as technical proficiency will undoubtedly bring a sense of purpose and fulfilment to employees.
As the manufacturing sector continues to evolve, embracing the human-machine collaboration model championed by Industry 5.0 is paramount in creating a sustainable and prosperous landscape. By striking a harmonious balance between technology and human ingenuity, companies can position themselves at the forefront of innovation while creating a workforce that is engaged, empowered and equipped to thrive in the years to come.
By Marc Wren
Marc Wren is an OT cybersecurity manager at Axians UK – Industrial Cyber Security, based in Wokingham. With expertise in industrial cybersecurity and automation, he combines technical skills with project management and business acumen. When he’s not securing industrial systems, you’ll find him enjoying a round of golf or casting a line while fishing.
Find out how emerging tech trends are transforming tomorrow with our new podcast, Future Human: The Series. Listen now on Spotify, on Apple or wherever you get your podcasts.