A Closer Look At Electric Vehicle (EV) Battery Production And Its Complexities As Automakers Miss Financial Forecasts – Rail, Road & Cycling
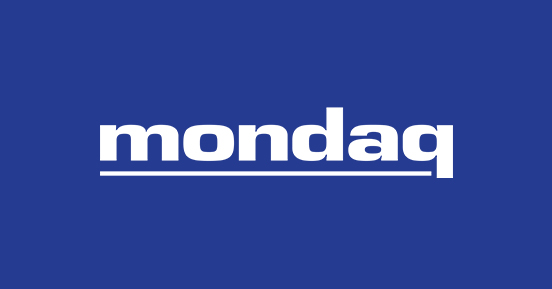
To print this article, all you need is to be registered or login on Mondaq.com.
The focus of this edition of the Automotive Industry Spotlight
is the mine-to-battery equation and the
‘green’ nature of EVs not being inherently
clear considering the greenhouse gas intensive nature
of battery manufacturing.
In industry news, Ford took a major hit on profitability
in the first quarter as it voluntarily delayed
deliveries of its F-150 models to solve production quality
issues. The International Union, United Automobile,
Aerospace and Agricultural Implement Workers of America (UAW) won a
major victory at Volkswagen’s Chattanooga
plant as its workers voted to
unionize. Nissan announced significant cuts to its
full year profitability and sales guidance, citing missed
forecasts for volume and voluntary payments to suppliers.
In regulatory news, Ford recalled 457,000 Broncos and
Mavericks due to vehicles stalling, per the National
Highway Traffic Safety Administration (NHTSA). Tesla
reached a settlement with the family of a fatal crash victim
involving their autopilot system. A bill introduced by 18
Republicans to undo Environmental Protection Agency (EPA) tailpipe
emission standards failed to receive the required
votes to avoid 2030 to 2032 EV-light vehicle sale
targets.
Industry Focus — The EV Battery Lifecycle
The rapid growth of EVs in the United States has placed
significant strain on the automotive supply chain and,
specifically, the sourcing of critical minerals for EV battery
development. Federal regulations have tightened requirements for
mineral sourcing for automakers, particularly as they apply to tax
credits for consumers purchasing EVs.
Changes in mineral sourcing requirements have led to significant
shifts in sourcing capabilities and industry ramp ups throughout
the automotive supply chain, presenting a significant remaining
hurdle for automakers hoping to achieve profitable EV business
units.
EV batteries and their assembly processes also still carry
significant carbon footprints from mineral extraction processes and
electricity sources. Significant questions remain on the resale and
recycle market for EV batteries — a key point for consumers
and automakers alike.
Where does my battery come from, and from what is it
made?
A vast majority of EVs worldwide are powered by lithium-ion
batteries, which are used for their high capacity and minimal
energy loss. A typical EV battery includes four key
minerals:
Supply chain considerations for automakers are conceptualized
under a ‘mine to battery’ roadmap. In its current form,
the mining and processing supply chain for lithium-ion batteries is
heavily globalized:
Recent legislation has put geopolitically-driven regulations in
place for critical mineral sourcing for use in EVs. In 2024, 40
percent of the value of “the critical minerals contained in
the battery must be extracted or processed in the United States or
a country with which the United States has a free trade agreement
or be recycled in North America” per the Inflation Reduction
Act. This would exclude minerals extracted or refined in China,
which currently controls a significant portion of the global
critical mineral refinement market. As a result, critical mineral
extraction has ramped up considerably in the United States and
Australia.
A greener footprint, but ‘end of life’
challenges remain
With the current state of mineral extraction, refinement and the
power sources fueling the U.S. electric grid, the
‘green’ nature of EVs is not inherently clear. Because
the process to manufacture EV batteries is more greenhouse gas
intensive than an internal combustion engine (ICE), a typical EV
requires a driver to drive between 15,000 and 25,000 miles before
net emissions benefits are realized. For the average American, this
is achieved in 18 to 36 months.
While recycling processes for EV batteries are still new and
remain labor intensive, some of the critical minerals in the
battery retain considerable value: Nickel and Cobalt can be
recovered at such a high rate out of ‘end of life’
batteries that they could considerably reduce the future demand for
mineral extraction. Safety concerns for dismantling lithium-ion
batteries at end of life — which is estimated to be 200,000
miles — are abundant; without proper oversight or care, the
batteries can catch fire and present significant danger to landfill
sites or recycling crews.
Cost burden remains, with no real end in
sight
While the environmental benefits of an EV are taking clearer
shape for consumers, cost challenges with the evolution in mineral
sourcing processes for batteries continue to take a toll on
automakers. The primary difference in the manufacturing cost
profile for EVs is the lithium-ion battery compared to a
traditional ICE. While the cost of an EV engine can vary based on
its composition of critical minerals, their cost compared to their
ICE counterparts varies materially. For a new Cadillac Escalade IQ
EV estimated cost per powertrain battery is approximately $22,500;
by contrast, a new Escalade ICE is estimated to cost approximately
$8,000. The cost difference to produce those batteries is
contributing to significant losses for domestic automakers; In
2023, Ford lost an estimated $40,525 per EV sold.
Mineral sourcing requirements, while designed to improve
longer-term supply chain prospects, will lead to continued near-
and mid-term cost challenges for automakers. With rapidly changing
supply chain sources for critical minerals and billions of dollars
committed to ramping up battery production domestically, the path
to profitability through streamlined lithium-ion battery
manufacturing remains steeply uphill.
Additional April insights are
included below.
Industry Update
March inventory levels ended at 2.58 million units, an
83,000-unit increase from February. Days’ supply closed at
47, approximately 7 percent above the five-year average. Inventory
at the Detroit 3 led the way for the U.S., with a 67,000-unit
increase in inventory, driven by an increase in light trucks.
Regulatory Landscape
Tesla Cybertruck Recall: The automaker
announced it would recall all of its 2024 model Cybertrucks
following reported issues that accelerator pads may dislodge and
become stuck in the car’s interior trim, cutting torque on
the accelerator and brake pads. The company has previously delayed
deliveries of the vehicle model due to issues with the accelerator
pedal.
NHTSA announces recall of 457,000 Ford
vehicles: Ford is recalling 457,000 Bronco Sport and
Maverick vehicles due to a defect in which the vehicles are unable
to start, or they stall when coming to a stop.
Bill to undo EPA tailpipe emission standards fails to
pass the Senate: The bill, introduced by Senator Mike
Crapo (R – Idaho) and co-sponsored by 17 Republicans, sought
to dismiss the final EPA policy towards tailpipe emission
standards. After intense negotiation with industry leaders, the EPA
settled on EVs to make up 30 to 56 percent of light-vehicle sales
by 2030 to 2032, where it had originally planned 67 percent. The
bill to undo the revised emission standard was voted down 52 to 46,
falling short of the 60 votes required to pass.
Originally published 30 April 2024
The content of this article is intended to provide a general
guide to the subject matter. Specialist advice should be sought
about your specific circumstances.