Disney’s innovative solution for flying robots
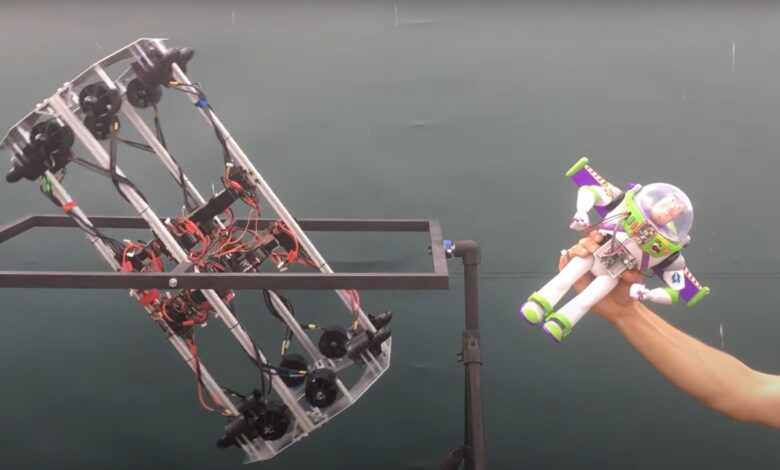
New-age storytellers use an innovative mixture of art, science, and technology to create immersive experiences.
To aid in such endeavors, engineers from Disney Research’s robotics team have devised innovative solutions that give a soft landing to various flying robots and equipment used in the entertainment industry.
The team has released videos showcasing different technologies in action, including stick-shaped robots with thrusters and water rocket propulsion.
Such advancements help Disney present its characters more realistically, especially in performing stunts in movies and theme parks.
Mastering aerodynamic precision
In Disney’s first video, a slender, stick-shaped robot is featured, and four ducted fans are arranged atop its structure. Equipped with a piston-modeled foot, the robot adeptly cushions the shock of minor descents.
Following this, the ducted fans swiftly act, stabilizing the robot by balancing unwanted deviations through precise aerodynamic thrust adjustments.
In a piece on IEEE Spectrum, Morgan Pope, a research scientist at Disney Research Center in Glendale, California, provides insights into the systems at play. Pope explains that the upright demonstration highlights the versatility of utilizing air resistance beyond just freefall scenarios.
Unlike traditional walking or hopping robots, which are reliant on ground contact for stability, Disney’s robots leverage aerodynamic forces, which, though gentler, effectively maintain balance.
According to Pope, this soft yet efficient approach not only facilitates standing but also suggests the potential for running or hopping robots to adopt flight phases, simplifying leg design and possibly enabling faster bipedal motion.
A somewhat bigger robot attempts a far more dramatic fall from 65 feet in the air in the next video. This is a small machine with a similar array of ducted fans on top and two piston-like feet.
As the robot descends, the fans serve a dual purpose: stabilizing its orientation in mid-air and upon landing. Each foot houses a plug of compressible foam designed for single use. Upon impact, the foam compresses, offering a consistent force profile that optimizes energy dissipation per unit of contraction.
“In the case of this little robot, the mechanical energy dissipation in the pistons is less than the total energy needed to be dissipated from the fall, so the rest of the mechanism takes a pretty hard hit. The size of the robot is an advantage in this case, because scaling laws mean that the strength-to-weight ratio is in its favor,” said Pope in IEEE Spectrum.
Mid-air halt and control strategy
The following demonstration done by the team shows the modulation of thrust required to control the orientation of larger robots.
Most aerial robotics applications rely on a system that can sustain the robot’s entire weight to offer control. It’s not necessary to be able to hover in our situation, according to Disney Research.
In this setup, the robot may spin freely since it is supported by a gimbal. Ducted fan arrays are installed at the extremities. The fans have a great deal of control over the orientation, but not enough force to keep the frame in the air.
As seen in the footage, complex robots are less likely to escape undamaged when subjected to the extraordinarily high accelerations of a direct earth impact.
In the last video, the team amalgamated previous techniques while introducing a striking new feature: a dramatic mid-air halt.
While ducted fans play a role, the primary method for high-speed deceleration involves a substantial water rocket. As a result, the mechanical legs manage only the final ten feet of dropping acceleration.
According to Pope, utilizing either water or rocket fuel, rockets operate on the principle of ejecting mass at high speed, generating a reaction force as per Newton’s third law. To optimize flow rate and response time, engineers used a wide nozzle design with rapid opening was crucial, achieved using copper foil and a custom punch mechanism.
The robot is able to maintain a steady hover approximately ten feet above the deck once the water rocket has brought it to a halt in midair thanks to the ducted fans. The robot falls again as they cut off, with the legs taking the brunt of the force.
“It might not be so obvious as to what this can be directly used for today, but these rough proof-of-concept experiments show that we might be able to work within real-world physics to do the high falls our characters do on the big screen, and someday actually stick the landing,” said Tony Dohi, the project lead at Disney Research, in the article on IEEE Spectrum.
The team claims that it has mutiple challenges still left to address. Typically, characters feature hinged legs instead of piston-like compression and don’t sport belts or ducted fans.
Pope highlights that, apart from concerns regarding packaging and aesthetics, ensuring precise landing locations raises intriguing considerations for perception and control. However, the team at Disney Research is confident of finding solutions to these.
ABOUT THE EDITOR
Jijo Malayil Jijo is an automotive and business journalist based in India. Armed with a BA in History (Honors) from St. Stephen’s College, Delhi University, and a PG diploma in Journalism from the Indian Institute of Mass Communication, Delhi, he has worked for news agencies, national newspapers, and automotive magazines. In his spare time, he likes to go off-roading, engage in political discourse, travel, and teach languages.