Inventor Says AI Is Ideal Partner For Developing Flexible Shape Digitizing Sensors For Soft and Continuum Robotics
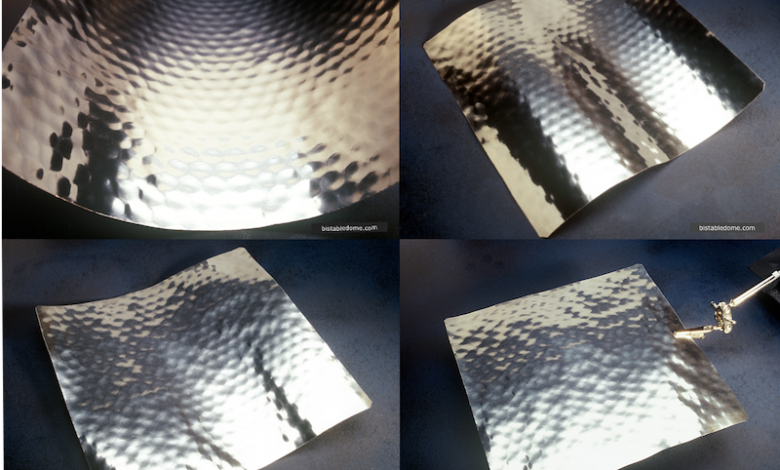
“AI is a perfect tool for using digital OBD patterns for object identification and measuring curvature, displacement, impact, force, motion, pressure, timing, position, weight, and fluid motion, for instance,”
NEW YORK, NY, June 04, 2024 /24-7PressRelease/ — The website bistabledome.com explains how very shallow flex actuated overlapping bistable domes, or OBDs, can be used to create unique low cost paper thin shape digitizing sensors for soft and continuum robotics, prosthetics, rehabilitation, sports training, and more.
Two patents were granted to Paul Ericson for using rows of OBDs to sense surface flexure and for a simple pump that pumps when bent. The website bistabledome.com explains those OBD applications as well as how they can be used to stiffen and shape thin strong metals.
“Flex actuated overlapping bistable domes are very shallow and formed in thin materials such as high strength steel. They create structures that are considerably stiffer than the original material but only 2 or 3 times as thick in profile,” says Ericson.
Shape sensor:
The website explains that the material through the centers of a row of overlapping bistable domes is functionally longer than the material along the edges and wants to occupy a larger radius.
“As long as flexural forces are not absorbed in the OBD material and the edges of the OBD row are contained within minimum radius limits in a stiffer flexible construction it can’t be bent without forcing OBDs toward the outside of the curvature in numbers proportional to curvature. When turned into switches they can indicate where, how much, and which direction from flat the sensor is bent. It may be the only bend sensor with true 2D capabilities,” suggests the inventor.
The bistabledome.com website demonstrates low resolution OBD sensor prototypes. Independent parallel 2D sensors are used for 3D shape sensing.
Artificial intelligence and OBDs:
“One bistable dome is a very simple structure but overlapping interconnected rows and arrays get complicated. Years ago some car companies considered OBDs for air bag seat sensors but there was no AI then. AI makes pattern recognition much easier and can speed up development of all OBD applications with predictive modeling, simulation and experimentation, rapid prototyping, and material research. And OBD products will expand uses for AI chips,” Ericson predicts.
“AI is a perfect tool for using digital OBD patterns for object identification and measuring curvature, displacement, impact, force, motion, pressure, timing, position, weight, and fluid motion, for instance,” says Ericson.
According to Ericson OBDs can be turned into on/off contact switches in a low cost paper thin flexible circuitry construction. “OBD sensors can be included in and protected in flexible materials for a wide range of applications,” he says.
The website suggests many applications including softer, safer robots, robot grippers, smart tires and safety bumpers, measuring pressure and position for advancing prosthetics, rehabilitation and gait analysis tools, car seat sensors for triggering airbags, athletic and sports training tools, identification and security sensors, and more. It suggests low resolution applications from smart beds and carpets to sailboat sails.
“OBD sensors can also complement and help calibrate remote sensing and open possibilities where remote sensing is impractical or impossible,” claims Ericson.
OBDs for stiffening and shaping thin high strength steel, fighting climate change:
According to the website 2D arrays of closely packed equally bistable OBDs can stabilize in a wide range of shape, within minimum radius limits. OBDs with a bias for one side can be used to force flat materials into desired shape, from simple tubing to 3D shape, as demonstrated at bistabledome.com.
“AI will make it much easier and faster to design and manufacture OBD arrays, which may be well suited for the gentle curves common in transportation related applications. Laminates of OBD layers can be very strong for their weight and could help reduce structural framing for vehicles, boats, containers, etc. OBD arrays can help reduce weight, increase fuel efficiency, and fight climate change,” says Ericson.
According to Ericson OBD stamping pressure is relatively low for high strength materials because they are stamped incrementally starting at an edge and distortion is incorporated in surrounding OBDs. “That means common 3D printing materials can be used for tooling, speeding up prototyping and development,” says the inventor.
Ericson believes an impact printer stamping OBDs of different characteristics could produce a wide range of curvature and shape and reduce tooling requirements.
A pump that pumps when bent:
OBD pumps are very simple and made with a single OBD or a row of OBDs, a flexible housing, and check valves. They can be made in a wide range of scale and utilize natural or mechanical motion to pump. Ericson believes large OBD pumps can use water motion for erosion control, remove unwanted sediment, pump cool water over corals, and possibly desalinate saltwater.
The short video below demonstrates OBD behavior in rows and arrays.
For more information visit bistabledome.com.
# # #