Pioneering Precision: The Fusion of AI Vision and Cobots in Manufacturing
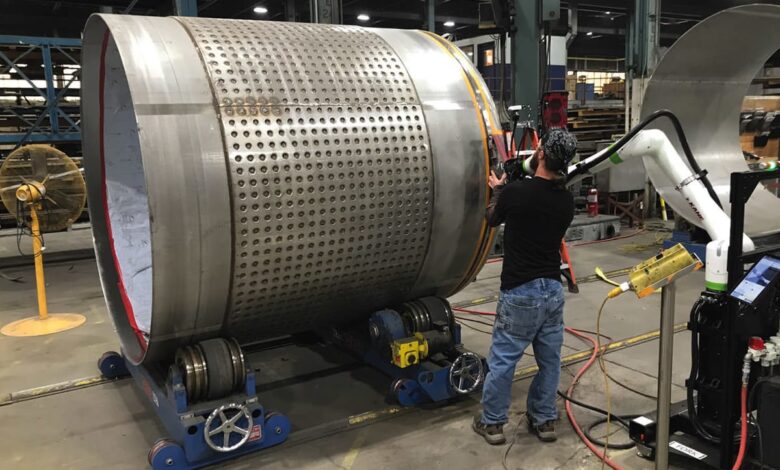
The integration of collaborative robots, or cobots, into manufacturing has revolutionized traditional processes, offering an unprecedented blend of precision, productivity, and safety. Known for their effectiveness in activities from palletizing to welding, cobots are emerging as invaluable assets for activities involving material removal like sanding, grinding and polishing, relieving human workers from arduous and risky tasks.
Now, with advancements in artificial intelligence (AI) and visual detection systems, cobots are evolving further, equipped to adapt their actions based on visual cues — a development poised to redefine efficiency and safety in manufacturing.
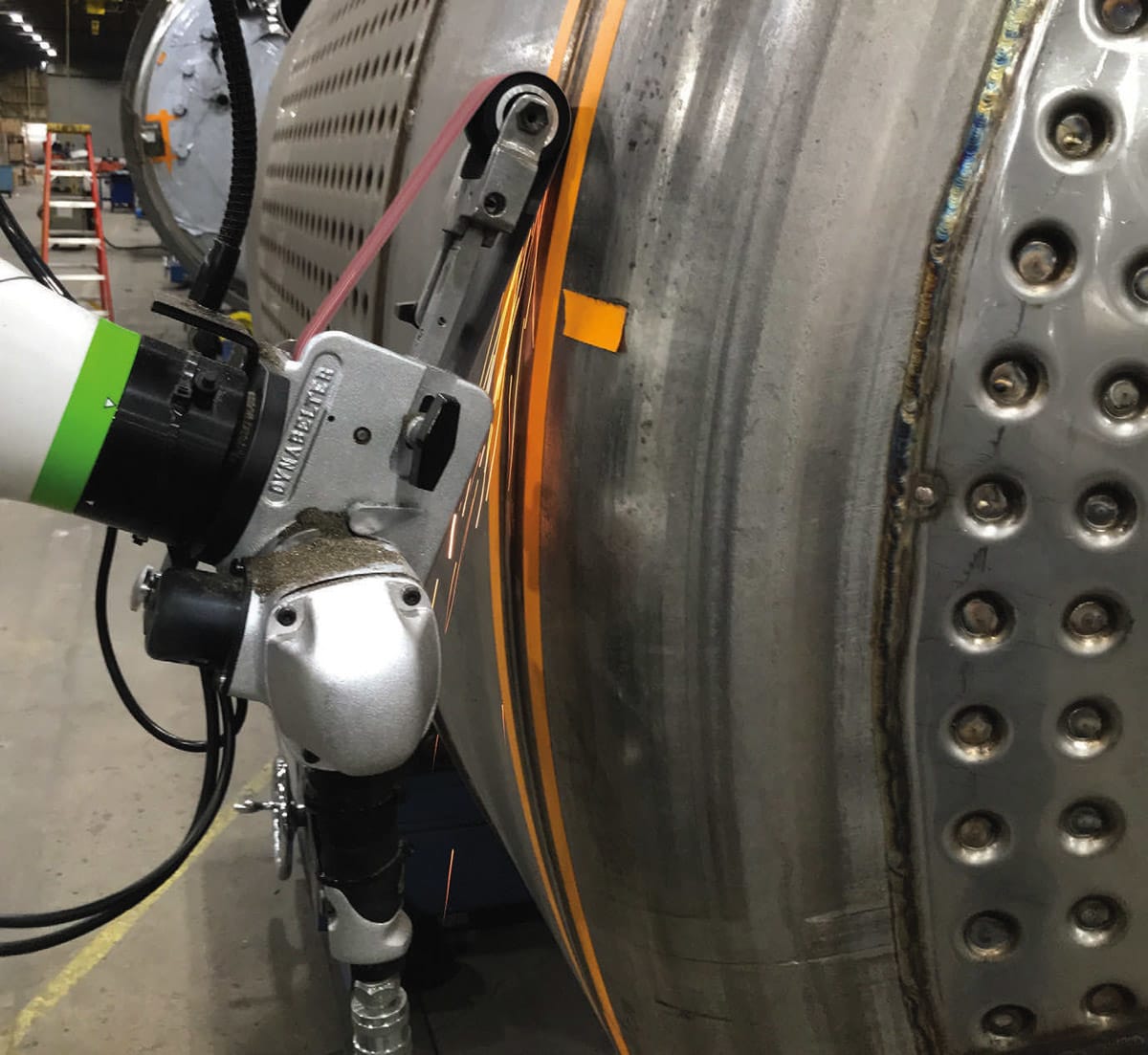
Kane Robotics, a developer of collaborative robotic solutions for material removal, finds itself at the forefront of this technological wave through its collaboration with the Paul Mueller Company, a stainless steel equipment manufacturer based in Missouri.
Paul Mueller Co. specializes in fabricating large tanks essential for diverse industries such as chemical processing, beverages, and oil and gas. Among its critical manufacturing processes is weld grinding, a laborious task involving manually smoothing weld seams post-welding. This activity, especially daunting for long welds on tanks ranging from 12 to 20 feet in diameter, poses significant risks to workers’ health and productivity due to injuries and fatigue.
In late 2023, seeking a sustainable alternative to manual weld grinding, Paul Mueller turned to Kane Robotics and its GRITTM cobot. The GRIT cobot, a mobile, cost-effective solution armed with a variety of preprogrammed end-of-arm tools including metal grinding capabilities, promises to revolutionize the task.
Kane Robotics engineers seamlessly integrated the GRIT XL cobot into Paul Mueller’s manufacturing line, harnessing its versatility and ease of installation. Equipped with a specialized weld-grinding end-of-arm tool, the cobot was programmed to execute precise grinding maneuvers over weld seams.
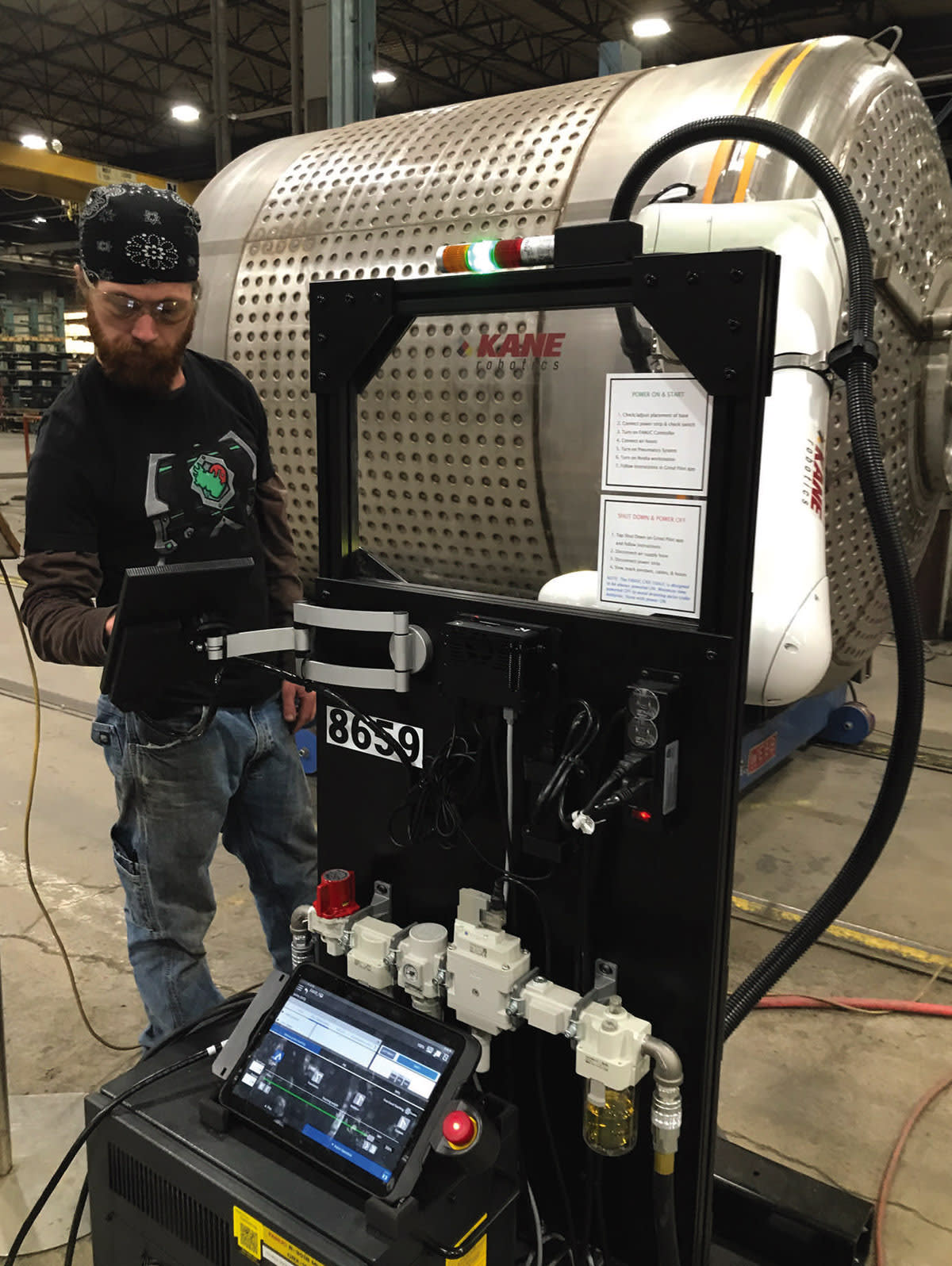
Thanks to its user-friendly interface, human operators quickly learned to configure the cobot. With the assistance of Kane Robotics engineers, the company completed the installation within hours and achieved full operation in just days.
The real breakthrough, however, lies in the incorporation of Kane’s ground-breaking GRIT Vision System. This AI-powered visual system, leveraging cameras and Kane’s proprietary machine-learning software, endows the GRIT cobot with the ability to detect and track uneven surfaces, such as weld seams, with unprecedented accuracy.
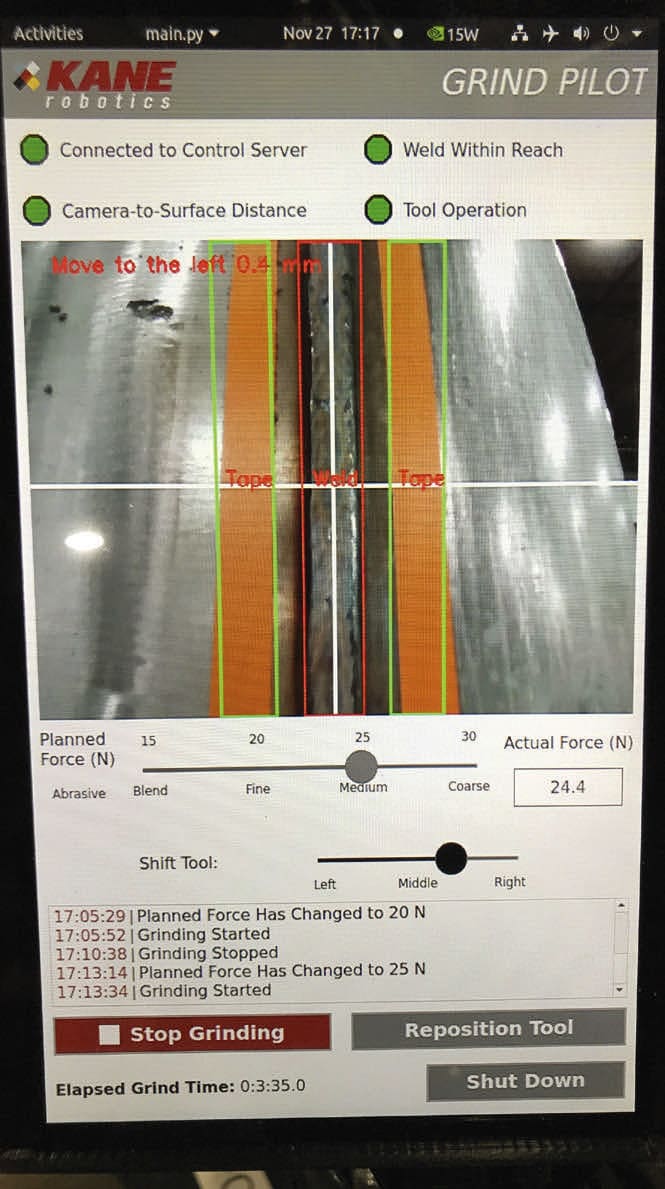
As the camera captures real-time data about the weld seam’s trajectory, the AI software dynamically recalibrates the cobot’s movements, ensuring precise grinding even on irregular surfaces. This advanced vision system, continually learning and refining its capabilities through accumulated data, promises unparalleled efficiency in material removal tasks.
The results of implementing the GRIT cobot solution coupled with the GRIT Vision System at Paul Mueller have been nothing short of transformative. Reported decreases in injuries and downtime coupled with heightened job satisfaction among manufacturing teams underscore the tangible benefits of this innovative approach.
As the partnership between Paul Mueller and Kane Robotics continues, ongoing feedback and data exchange pave the way for further enhancements and refinements. Suggestions for improvements, such as incorporating operator-defined parameters into the AI interface, reflect the collaborative spirit driving this technological evolution.
The success story of Kane Robotics’ intelligent, AI vision-equipped cobot solution at Paul Mueller Company exemplifies the transformative potential of smart automation in manufacturing. By mitigating fatigue-related injuries, enhancing efficiency and improving working conditions, this synergy of AI and robotics heralds a new era of productivity and safety.
This article was written by John Spruce, CEO, and Arlo Caine, Robotics Engineer, both at Kane Robotics (Austin, TX). For more information, visit here .