Turmec launches Aftersales CRM system
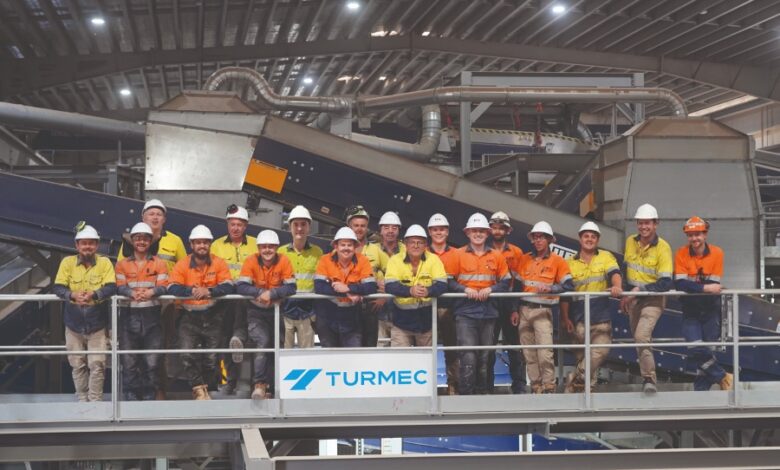
The Turmec team behind a world-first recycling facility in Brisbane. Image: Turmec
Turmec launches new Aftersales CRM system, the next generation of rapid solutions providing customers with one central place to order spare parts and services and achieve a faster response time.
Turmec has lead the way in recycling innovations with turnkey solutions for waste management, exemplified by a world-first project in Brisbane.
With more than 50 years’ experience in the engineering and recycling industries, it’s now setting new benchmarks in aftersales solutions, with what’s been described as the fastest response time in the marketplace.
All future Turmec projects will have the aftersales CRM system as standard, with QR codes fitted, meaning there will no longer be delays in ordering, training or fitting spare parts.
Robert Thornton, Turmec’s Supply Chain and Aftersales Director, says the new Turmec aftersales CRM system will provide clients with a quicker response time and access to search, find and order parts 24/7, providing next generation service.
Key features include: easier ordering parts verified to fit customers’ assets; scanning QR code to instantly access verified-to-fit parts; 24/7 access to parts ordering and service request; and general support resources, including manuals and PPM’s.
“In our commitment to enhance our customer experience, we are thrilled to announce the implementation of the cutting-edge Turmec CRM system,” Robert says.
“With this innovative system, each plant will now feature a distinctive QR code, making part identification effortless and re-ordering a breeze.
“By simply scanning a QR code, clients now access detailed information about the machine, including its documents and the various parts.”
TURNKEY PROCESS
Turmec offers planning, design, manufacturing, installation and support to waste and recycling management companies globally.
From a base in Gaeltacht at Rathcairn, Co. Meath, an in-house team of engineers and designers offer a complete turnkey process, from conceptual drawings to a fully operational plant, for bespoke plants through to solutions for new or existing plants, and general engineering projects.
In 2018, 2019, 2023 and 2024, Turmec won various awards for its work, most notably Irish Exporters Awards (medium-sized business), Manufacturing Company of the year from Chambers Business and Irish Steel Association.
Geoff Bailey, Turmec Chief Executive Officer, says the team is proud to announce the launch of the aftersales CRM system, leading the way in the aftersales market within the industry.
He says team Turmec is dedicated to finding the best recycling engineering solutions for client requirements, with tried and tested approaches, combined with design expertise, to address specific requirements.
The goal is to create systems that minimise labour input while consistently extracting high-quality recyclables, achieving maximum throughput with minimal maintenance.
WORLD FIRST
One of Turmec’s key projects is the Turmec/Rino project, the world’s largest state-of-the-art construction waste processing facility in Brisbane.
Geoff says this project is a testament to Turmec’s commitment to sustainable waste management and its ability to deliver large-scale, complex projects.
The €30m project began in March 2022 with a timeline for completion by November 2023. The facility processes construction and demolition (C&D) and commercial and industrial (C&I) waste, with a processing capacity of 475,000 tonnes per hour. It’s a world-first, able to sort through wet and dry waste under one roof.
Upon completion of the plant, Dan Blaser, Rino Recycling General Manager, said the company had scoured the globe and “brought together the best engineers in the world to successfully deliver a leading plant that underpins a strong sustainable recycling industry for Australia”.
Geoff says the project is Turmec’s largest, by scale, in its long history in the supply and installation of mechanical treatment plants worldwide.
“Our expertise and knowledge made us the ideal candidate for this project, which is the biggest mixed construction and demolition plant in the world by volume,” he says. “The solution Turmec created and installed, in collaboration with wet plant specialists CDE, means that varied waste types can be integrated into an automated production line which effectively separates out the materials allowing for the production of a number of high-quality products such as aggregates and road base. The residual waste can be used as fuel for industrial boilers.”
For more information visit: www.turmec.com