Autonomous & Self-Driving Vehicle News: Hyundai, Plus, Kodiak Robotics, Roboworx, TIER IV & Scania
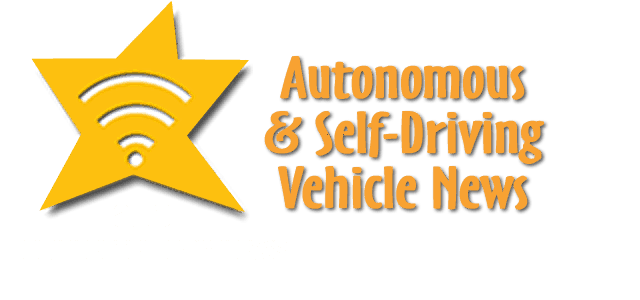
In autonomous and self driving vehicle news are Hyundai, Plus, Kodiak Robotics, Roboworx, TIER IV and Scania.
Hyundai & Plus Autonomous Driving for Class 8 Hydrogen Truck
Hyundai Motor Company (Hyundai Motor) and autonomous driving software leader Plus today unveiled the first Level 4 autonomous Class 8 hydrogen fuel cell electric truck in the U.S. at the Advanced Clean Transportation (ACT) Expo, the largest advanced clean transportation technology and fleet event in North America.
A result of the collaboration between Hyundai Motor and Plus, Hyundai Motor’s XCIENT Fuel Cell truck, equipped with Plus SuperDrive™ Level 4 autonomous driving technology, is on display at the Plus ACT Expo booth (#2044).
The Level 4 autonomous XCIENT Fuel Cell truck is undergoing initial autonomous driving assessments in the U.S., making it the first-ever Level 4 self-driving test on a Class 8 fuel cell electric truck to take place in the country. The collaboration seeks to show that autonomous hydrogen fuel cell trucks can help make trucking safer, more efficient, and more sustainable.
“We are excited to showcase our collaboration with Plus to test Level 4 autonomous driving technology with our Class 8 XCIENT Fuel Cell truck,” said Martin Zeilinger, Executive Vice President and Head of Commercial Vehicle Development at Hyundai. “Hyundai Motor has been driving the energy transition paradigm with our advanced fuel cell technologies. By adding autonomous capabilities to our world’s first mass-produced hydrogen-powered XCIENT Fuel Cell truck, Hyundai is looking forward to providing fleets and vehicle operators additional solutions that enhance road safety and freight efficiencies thanks to Plus’s industry-leading autonomous driving technology.”
First introduced in 2020, Hyundai Motor’s XCIENT Fuel Cell truck has conducted commercial operations in eight countries worldwide, establishing a successful track record of real-world applications and technological reliability.
At last year’s ACT Expo, Hyundai introduced XCIENT Fuel Cell tractor, the commercialized Class 8 6×4 fuel cell electric model, powered by two 90kW hydrogen fuel cell systems and a 350kW e-motor, providing a driving range of over 450 miles per charge even when fully loaded.
Plus’s SuperDrive™ solution is being deployed across the U.S., Europe, and Australia. The system uses a combination of cutting-edge sensors, including LiDAR, radar and cameras, to provide surround perception, planning, prediction and self-driving capabilities.
“We are thrilled to collaborate with Hyundai Motor Company on this important initiative to create more sustainable and safe transportation options. A decarbonized future with autonomous hydrogen fuel cell electric trucks that also improve safety and efficiency is one that Plus is proud to support with our cutting-edge autonomous driving technology,” said Shawn Kerrigan, COO and Co-Founder at Plus.
Hyundai Motor and Plus have released a video highlighting their collaboration, which can be seen here: https://www.youtube.com/watch?v=_d19h_v7abo.
Kodiak & Chang Robotics
The world’s most powerful industrial Battery Electric Vehicle (BEV) is fast becoming a reality, thanks to the alignment of Kodiak Technologies, Chang Robotics, and design and engineering technology from Roush. As anticipated, Kodiak and Chang have designed and unveiled the product and business plan for their American-made heavy duty Hybrid Electric Vehicle (HEV) for commercial and industrial snow removal at the recent Snow Symposium summit in Buffalo, NY.
Following the launch, more than 35 airports are now in talks to become the first to order and implement the ultra-powerful vehicles anticipated to premiere in early 2025. Many more airports—and multiple additional public and government locations and sectors—are planning to follow suit, with the help of federal and municipal incentives that will help to fund the infrastructure and initial costs.
According to Kodiak Technologies board member Matthew Chang, the power output of the new hybrid and electric vehicle makes it the most powerful vehicle ever made, capable of a total torque output exceeding diesel-powered vehicles. The total vehicle power output exceeds two15-liter turbo-diesel engines.
“These new offerings include an HD BEV and a series hybrid BEV capable of more instantaneous power output than a twin diesel engine vehicle, making it more powerful than any other pure battery electric vehicle on the market,” he said.
According to Chang, “We knew the vehicle was exceptionally powerful and that we were testing the limits of component suppliers in the USA. After exhaustive research we could not find a more powerful vehicle with similar all-battery electric architecture. Other larger vehicles such as trains, mining equipment, and construction equipment that operate on electric drive train are not pure battery electric, as they utilize an AC power design or a parallel hybrid design.”
A New Horizon
The Kodiak Technologies design leverages technology and existing customer relationships from Kodiak America.The concept is particularly innovative in that it represents a platform design that can be transferred to multiple other vehicle types that require large power output, which has been a previous limitation for BEV’s. For areas where MCS (Megawatt Charging Standard) infrastructure is not available, the vehicle design includes a series hybrid option that can be powered by hydrogen, propane, biodiesel, or petrol-diesel to extend range and battery life when required.
The first Kodiak Technologies implementation is an FAA-compliant industrial snow blower vehicle capable of meeting FAA minimum requirements of capability to move 7,000 tons of snow per hour at operating speeds of 25MPH, which the team recently presented as a design and business case at the FAA Snow Symposium summit in Buffalo, NY. The Made-in-America distinction makes the vehicles eligible for federal grant programs including the bi-partisan infrastructure law (IIJA) and inflation reduction act (IRA). The first completed vehicle is under construction now and is expected to be ready for demonstration later this year.
Early Responses
More than 100 airport operators have previewed the new design and business case during the recent FAA presentation, and more than 35 airports departments of the federal government, and international airlines entered discussions with the Kodiak Technologies team.
Responses from airport operators included the following:
“We’re extremely pleased to be one of the first airports to view this design and to potentially be one of the first to deploy this exciting technology.”
“This successful design, created through the collaboration of well-known American partners such as Roush, marks a significant milestone in the industry. It creates what is perhaps the first and greatest opportunity yet for heavy duty vehicle users to migrate to a sustainable platform.”
A representative of one of the nation’s leading airlines remarked, “After a recent preview of the design, I’m highly impressed not only with the design of this new equipment but also with the technology roadmap and the future capabilities for this platform technology, which may impact the breadth of industrial EV equipment for many generations to come.”
Kodiak Robotics & Textron
Textron Systems Corporation, a Textron Inc. (NYSE: TXT) company, a leading developer of crewed and uncrewed military ground vehicles, and Kodiak Robotics, Inc., a leading self-driving technology developer for the trucking and defense markets, announced today that they are collaborating to develop an autonomous military ground vehicle specifically designed for driverless operations. Through this collaboration, Kodiak will integrate its industry-leading autonomous system, the Kodiak Driver, into a Textron Systems prototype, purpose-built uncrewed military vehicle. This collaboration also marks Kodiak’s first integration of its autonomous technology into a vehicle designed without space for a human driver.
Textron Systems has extensive experience in developing air, land and sea vehicles. The collaboration between the company, a leader in military ground vehicles, and Kodiak, a dual-use autonomous driving company for military and commercial applications, represents a unique model for bringing cutting-edge artificial intelligence (AI) powered, autonomous technologies to military customers. It also demonstrates the readiness of the Kodiak Driver for driverless operations as well as its adaptability to a diverse range of vehicle types, both on- and off-road.
The system being developed by the companies will operate using the same core technology that’s embedded within Kodiak’s autonomous long-haul trucks, which have been validated across nearly 3 million miles of real-world operations. The vehicle will also feature Kodiak DefensePods, an adapted version of Kodiak’s modular, swappable SensorPods, designed for military use. DefensePods are pre-calibrated, pre-built hardware enclosures that include the sensors necessary for autonomous driving. A technician without specialized training can swap out a DefensePod in the field in 10 minutes or less.
“Textron Systems has designed, developed and manufactured military ground vehicle systems for decades. Joining forces with Kodiak allows us to bring cutting-edge autonomous technology to our industry-leading uncrewed military ground vehicle systems, progressing the functionality, adaptability, reliability and ruggedness of our technologies,” said Textron Systems’ David Phillips, Senior Vice President, Land and Sea Systems. “Integrating our vehicle with Kodiak’s AI-powered autonomy software and pioneering modular DefensePods represents a major step forward in delivering a mission-ready autonomous system.”
The companies intend to integrate Kodiak’s technology into the Textron Systems uncrewed military vehicle and demonstrate driverless operations later in 2024. Afterwards, Textron Systems and Kodiak intend to jointly explore future opportunities with both the U.S. DoD and the militaries of other allied nations, as they look to accelerate automation into military ground vehicles. Deploying uncrewed vehicles to perform high-risk and complex tasks in the field will assist the U.S. military in removing servicemen and women from harm’s way, while enhancing national security.
“The future of autonomous military ground vehicles is dual-use technology developers like Kodiak working with industry leaders like Textron Systems,” said Don Burnette, founder and CEO, Kodiak. “Collaborating with Textron Systems will allow us to showcase the capabilities of Kodiak’s AI-powered, driverless technology in military, off-road environments. Together, we can bring new capabilities to ground systems, supporting the warfighter at the speed of relevance.”
Kodiak’s collaboration with Textron Systems builds on the company’s expansion to diversify applications of the Kodiak Driver for military vehicles. In December 2023, Kodiak unveiled its first autonomous test vehicle designed specifically for the DoD, a Ford F-150 upfit with Kodiak’s autonomous technology.
Textron Systems has over three decades of experience in uncrewed land, air and sea systems, from design to integration to production. Having supported multiple military programs of record, Textron Systems builds on a mature, proven history in supporting the DoD and our allies. By collaborating with Kodiak, Textron Systems gains access to industry-leading autonomy capabilities, alongside its deep expertise in crewed and uncrewed vehicles.
Roboworx & Picnic Works
Seattle-based Picnic Works, Inc., (Picnic) a global leader in food production automation, and Roboworx, a subsidiary of Administrative Resource Options Inc. (ARO), today announced a strategic collaboration to facilitate the national rollout of Picnic’s fleet of autonomous Picnic Pizza Stations. This partnership aims to enhance the efficiency and consistency of pizza production across numerous restaurant locations.
Founded in 2016, Picnic has been at the forefront of integrating technology with food service. The Picnic Pizza Station is designed to seamlessly fit into existing commercial kitchens, assembling 130+ pizzas per hour, depending on size, with precision and efficiency. Recognized as a Kitchen Innovation Winner by the National Restaurant Association, Best in Show at CES, and listed in the FoodTech 500, this innovation is set to revolutionize operations in restaurants, live event venues, convenience stores, universities, convention centers, corporate campuses, and other food service venues.
“At Picnic, our expertise in food and technology drives us to constantly innovate,” said Michael Bridges, CEO of Picnic. “To ensure the seamless deployment and support of Picnic Pizza Stations across the country, we sought out a dedicated partner. Finding Roboworx, with their exceptional automation expertise, perfectly aligns with our mission to help our customers thrive.”
Roboworx, dedicated to the service, support and customer success of robotics, will deploy the Picnic Pizza Stations and provide ongoing support and preventive maintenance. This collaboration ensures that the devices remain operational and efficient, allowing Picnic’s customers to focus on their core business activities without the distraction of managing advanced robotic systems.
“In a world where robotics continually enhance our lives, the Picnic Pizza Station stands out as a truly unique and groundbreaking innovation that delivers faster, more consistent and more convenient pizza production,” said Chris McNelis, vice president of operations, Roboworx. “Our team of automation experts at Roboworx will provide 24/7 remote monitoring, preventive maintenance, and any break/fix support to ensure the Picnic Pizza Stations are working properly so Picnic’s customers can focus on running their businesses, not managing their stations. We’re all about customer success.”
TIER IV Robotaxi Service
TIER IV, a pioneer in developing open-source software for autonomous driving (AD) systems, is set to launch a unique robotaxi service in November 2024. Initially targeting areas and times that conventional taxi operators struggle to serve, the service will begin with proof of concept (PoC) tests in the Tokyo Bay area of Odaiba. The goal is to gradually expand to cover major districts in Tokyo by 2025 and the entire metropolitan area by 2027. TIER IV strives to foster a harmonious coexistence between new robotaxi services and existing mobility ecosystems.
TIER IV has developed multiple classes of the reference design for developing AD systems based on Autoware*1. The reference design presents appropriate vehicle models and environments, often referred to as operating design domains (ODDs), in which AD systems are verified and validated to be functional, utilizing TIER IV’s software platforms.
For technical validation, the robotaxi reference design incorporated into the JPN TAXI vehicle model has achieved sufficient safety and availability, effectively defining ODDs even in heavy-traffic areas. Commercial applications have also been deployed successfully, leveraging several other variants that inherited from the robotaxi reference design, for public transportation networks nationwide and in-factory logistics.
Building upon these achievements, TIER IV is gearing up for the commercialization of new robotaxi services. PoC tests in Odaiba are set to pave the way for public access by November 2024, while ongoing discussions with transportation operators will ensure seamless integration into existing mobility ecosystems.
Looking ahead, TIER IV plans to expand these robotaxi services, ensuring safety and availability standards comparable to conventional taxis. Initially targeting key areas within Tokyo before expanding citywide, TIER IV remains committed to creating open innovation in the autonomous driving sector, one ride at a time.
Leopard Imaging Eagle 2 Camera
Leopard Imaging Inc. (Leopard Imaging), a global leader in intelligent embedded camera design and manufacturing, is to launch stereo camera EAGLE 2 LI-VB1940-GM2A-119H at Embedded Vision Summit 2024. This camera marks a significant milestone in the realm of vision technology as the world’s first RGB-IR high-resolution stereo camera with patent-pending features, poised to redefine day and night vision capabilities.
The Eagle 2 camera boasts a cutting-edge design, incorporating two automotive-grade 5.1-megapixel global shutter RGB-IR image sensors. This dual-sensor configuration enables unparalleled depth perception and spatial accuracy, essential for various applications ranging from autonomous vehicles to industrial automation, robotics, and AI-IoT systems.
One of the standout features of the Eagle 2 camera is its ability to deliver exceptional performance in diverse lighting conditions, thanks to its integrated RGB-IR sensor technology. By seamlessly blending visible light and infrared imaging, this camera ensures robust vision capabilities both during daylight hours and in low-light or nighttime scenarios. Whether navigating busy city streets or monitoring remote areas under the cover of darkness, the Eagle 2 camera offers unmatched versatility and reliability.
Moreover, two wide and narrow-angle IR dot pattern projectors further enhance depth perception and object detection, making the Eagle 2 camera a formidable tool for precise spatial mapping and 3D reconstruction tasks.
Founded in 2008, Leopard Imaging has supported thousands of well-known companies in advanced imaging solutions with its experienced engineering teams, high quality manufacturing capabilities in both “Made in U.S.A” and offshore, and quality management certifications such as IATF16949 for automotive industry, and AS9100D for aerospace industry.
Leopard Imaging is showcasing the demo of Eagle 2 at Embedded Vision Summit 2024 in Santa Clara Convention Center, Booth 704.
Scania Autonomous Mining Trucks
Scania starts sales of autonomous mining trucks, opening up for safer, more efficient and more sustainable mining operations.
The realization of autonomous transport is taking a big step forward as Scania opens up for orders of the company’s self-driving mining solutions. It is now possible to place orders for Scania’s 40-tonne autonomous heavy tipper for mining, with the 50-tonne model to follow shortly afterwards.
As a first step, Scania will start sales of its autonomous mining solutions in Australia, with first deliveries and start of operation scheduled from 2026. The next market in line will most likely be Latin America, a region where Scania has a significant market presence in the mining segment.
“The transition from research and development to the launch of a commercial product is a major milestone for us and for autonomous heavy transport in general. This is the most advanced product Scania has put on the market so far,” says Peter Hafmar, Vice President and Head of Autonomous Solutions at Scania.
Easier to go electric and to achieve sustainable mining
Mines have long been seen as one of the most promising environments for autonomous vehicles, as they can contribute to safer working conditions and more efficient operations.
Scania’s mining solutions with smaller, civil-class trucks also have overall potential advantages over the industry’s traditional heavy haulage trucks, both in terms of emissions and productivity. By utilising Scania’s autonomous mining trucks, the overall mining footprint including energy and infrastructure requirements can be reduced, meaning that capital and operating expenses may also be reduced at suitable sites.
Scania’s autonomous trucks can also be smoothly fitted into an existing operations set-up in a mine, thanks to their interoperability with other systems and vehicles.
“Another benefit with our solution is that it allows mining companies to more quickly take the next step towards zero-emission operations. It’s easier to electrify operations with Scania’s autonomous trucks compared with traditional heavy haulage trucks,” says Hafmar.
Developed in close cooperation with mining customers
Over the past ten years, Scania has invested heavily in the development of self-driving vehicles. Innovations include applications for hub-to-hub transport on highways as well as autonomous vehicles for confined areas such as mines.
Scania’s autonomous tipper truck has been developed in close cooperation between Scania’s R&D department and customers in the mining industry, with extensive testing in the harshest real-life conditions.
“It’s probably the most ambitious research and development project we have done so far together with a customer, and I am very pleased about the result. Thanks to all the rigorous checks and numerous on-site tests we have been able to develop an optimal autonomous transport solution for mines,” Peter Hafmar concludes.