Bringing Bio-Inspired Robots To Life – Eurasia Review
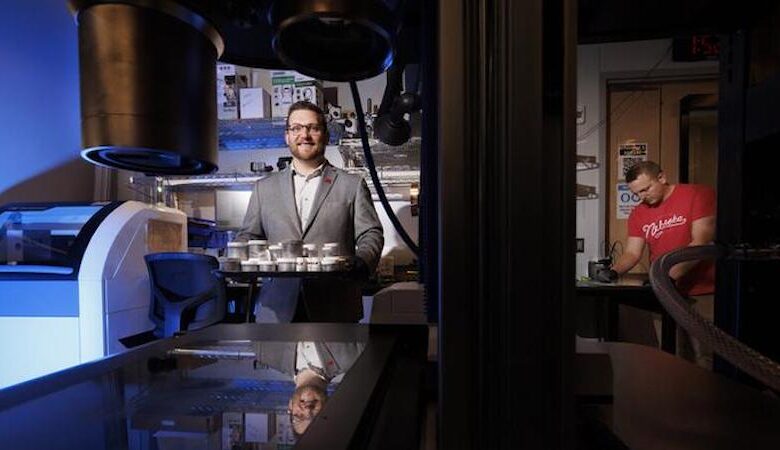
Engineers are increasingly eager to develop robots that mimic the behavior of animals and biological organisms, whose adaptability, resilience and efficiency have been refined over millions of years of evolution.
In bringing bio-inspired robots to life, scientists must first create soft matter counterparts that match the softness and functionality of biological tissue. University of Nebraska–Lincoln engineer Eric Markvicka is at the forefront of these efforts. He recently received a five-year, $690,000 grant from the National Science Foundation’s Faculty Early Career Development Program to advance work on a manufacturing approach that would produce a novel class of materials that could propel the fields of soft robotics, stretchable electronics and beyond.
It would be the first manufacturing strategy to yield stable mixtures of liquid metals with a wide range of solid particle additives to achieve enhanced properties — including thermal and electrical conductivity, fluidity and capacity for self-repair — that exceed anything on today’s market.
The composites would be suitable for use in additive manufacturing, commonly known as 3D printing, and would accelerate momentum toward 4D printing, which produces machines that can morph to adapt to different environments.
“At the end of this project, we’ll have a manufacturing strategy for creating diverse liquid metal mixtures that are appropriate for additive manufacturing,” said Markvicka, assistant professor of mechanical and materials engineering. “Such capabilities will enable the engineering of new materials for hybrid 4D additive manufacturing where we can create a number of things, from robotics to machines, that ultimately mimic biological organisms.”
Scientists have long recognized the commercial potential of liquid metals, which offer infinite mechanical failure strain and enhanced thermal and electrical conductivity compared to other elastomers or fluids. They also have the ability to repair themselves, similar to many natural organisms: Markvicka’s previous work shows that electrical circuits formed by liquid metal droplets can reconfigure after damage occurs.
To further enhance these properties, researchers have tried adding solid particles to liquid metals. But these efforts have run up against two major barriers. For one, most liquid metal varieties include gallium, one of the most highly reactive metals on the periodic table. Many additives, such as copper or aluminum, react with gallium in a way that transforms the mixture from a liquid to a solid, compromising the fluidic advantage.
When the additive doesn’t react with gallium, a different problem arises. The solid particles are enveloped in a thin oxide layer created by the liquid metal’s high surface tension. That layer allows the particles to be incorporated into the metal — but in the process, air voids form. These voids expand at higher temperatures, reducing the material’s thermal conductivity.
Markvicka’s strategy takes aim at both problems by adding an intermediate layer, or coating, to the additive particles. This nanoscale layer serves a dual purpose: For particles that would alloy, or mix, with gallium, it acts as a corrosion barrier, thwarting the reaction that would mitigate fluidity. For nonalloying particles, the layer acts as a wetting agent, enabling the material to integrate into the liquid metal without forming air voids.
Markvicka is one of just a handful of researchers nationwide who are exploring the use of coatings in liquid metal mixtures. If successful, the approach would enable engineers to make custom liquid metal mixtures with particular physical, chemical and rheological traits.
“Few have taken this interfacial engineering approach to not only protect the filler, in terms of the corrosion barrier that’s incorporated, but also develop the ability to take particles that don’t reactively wet and incorporate them,” he said.
Markvicka will also advance a new frontier in engineering education by emphasizing not just the technical side of the field, but also the business dimension. This “entrepreneering” approach merges entrepreneurial literacy with research-based education.
“We provide a mix of foundational and specialized technical courses; however, we rarely discuss economic impact or market viability when designing or creating new products,” he said. “In the rapidly changing job market, engineers who understand the entrepreneurial process are better positioned to seize opportunities and succeed in uncertain and complex situations.”
In concert with Nebraska’s Established Program to Stimulate Competitive Research, Markvicka will develop the first mobile science lab on manufacturing, which will integrate concepts from his research and entrepreneurial skills. It will be distributed to middle and high school students across Nebraska. Markvicka will collaborate with middle school teachers to help them incorporate the mobile lab into their classrooms.
On campus, Markvicka will integrate entrepreneering-based modules into traditional engineering courses, ensuring that a broader range of students are exposed to entrepreneurship principles.
“This isn’t just for people who are interested in starting a company or working for a startup,” he said. “These skills are also important for people working in industry. They need to know how you begin to vet and understand if an idea is viable commercially.”
The National Science Foundation’s CAREER award supports pre-tenure faculty who exemplify the role of teacher-scholars through outstanding research, excellent education and the integration of education and research.