Built for Industry 4.0
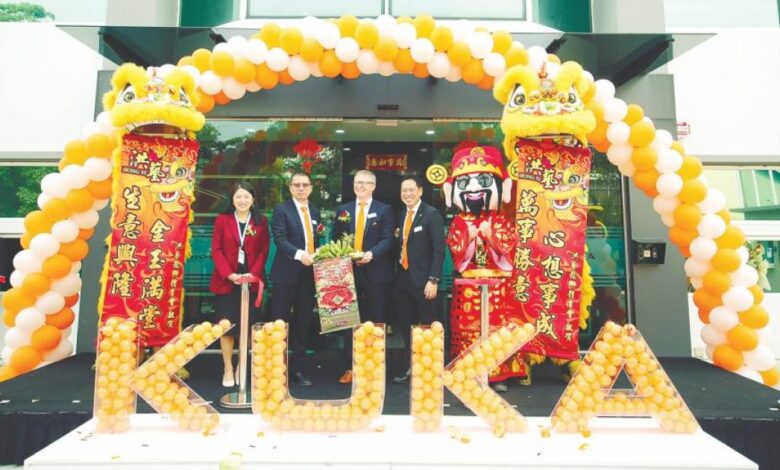
THE fascination with robots is evolving. One of the largest worldwide suppliers of intelligent automation solutions is German robot maker KUKA, whose robotics technology is now supporting a diverse range of industries in the Malaysian automation market.
KUKA’s capabilities and cutting-edge technologies are known for various applications such as palletising, welding, machine tending, simple assembly, pick and place, as well as training cells.
Priding itself on having all the right robots in its portfolio, KUKA’s machines have allowed it to provide customers with robots for a range of applications, from small assemblies in the furniture industry to side panels for freight cars.
Its welding robots, for instance, are for customers in the central manufacturing sectors of the automotive and metalworking industries. Unlike a human workforce, the robots are automated to complete complex welding tasks efficiently and furthermore, to implement them to perfection down to the tiniest weld seam with high system stability.
These robots visibly stand out for their significantly increased productivity due to integrated process steps, reduced cycle times and long maintenance intervals.
KUKA Asia-Pacific excluding China (APeC) regional CEO and KUKA Malaysia CEO Alan Fam said with KUKA’s intelligent automation products, productivity has been proven to rise, which in turn will affect profitability in the entire value chain.
The smart integration of its products into the digital and connected world of production does not stop at just the company’s welding robots, with KUKA having other robust and flexible robots suitable for a wide range of tasks.
Diverse portfolio
As much as the robots look like they are involved in heavy labour like welding and palletising, KUKA has robots that are capable of handling tasks in the food and medical field.
Robots such as the KR Cybertech HO and KR Iontec HO have food compatible H1 lubricants in all axes, which allow the products to meet the high, stringent requirements of the food industry for hygienic handling.
Other robots, like the LBR Med, are capable of executing diagnostics and surgical interventions on patients. KUKA even has a range of robots developed for a variety of cleanroom applications.
Designed for environments that need the highest levels of cleanliness and the lowest levels of particle emission without sacrificing speed or performance, KUKA’s robots are reliable and fast enough to achieve high productivity and quality manufacturing for industries such as life sciences, healthcare, medical devices, biotechnology and pharmaceuticals.
These robots can be used even in confined workspaces, as they can be mounted on the floor, ceiling, wall and at an angle.
Industrial Internet of Things
With Industry 4.0 in full swing, established structures are on the way out, with cyber-physical production coming in at full force. Via its Malaysian business entity KUKA Robot Automation, the group seems well-prepared for the change, with intelligent machines equipped with sensitivity and enhanced intelligence designed to work side by side with humans, while still operating more independently than before.
The fleet of products by KUKA are mobile, highly flexible and versatile for changing industries that are incorporating digital networking and autonomous adjustment to rapidly changing production requirements.
“It is easier to teach a cobot programming as compared to an industrial robot. It is also easier to integrate a cobot to any of the external devices. Because of these benefits, cobots are very popular and are used in many industries, such as automotive, manufacturing, electronics, warehousing and logistics,” said KUKA Robotics (APeC) senior business development manager Deric Chin at the launch of KUKA Malaysia office in Puchong last week.
A portmanteau of “collaborative robots”, cobots are another arm of KUKA’s products that are designed to work with humans in a shared space. Among many others, this splicing of value in both humans and robots is something KUKA sees that will drive growing productivity.
Both the robots and cobots by KUKA have made an indelible mark on companies that are using the products in Malaysia. A steel wire and wire mesh manufacturing company in Perak that uses KUKA’s products, Wei Dat Steel Wire, has witnessed the uptick in production firsthand.
“We are amazed by the performance of KUKA’s KR Quantec-2 robotic arm. With this automation in place, the entire steel wire bending process is faster and efficient. Previously, (we could) see 500 steel wire mesh bent in one day. It has now increased to 1,500 per day,” said an employee from Wei Dat.
KUKA is ready to support more Malaysian businesses to raise efficiency and automate operations as the country’s smart technology continues to grow.