Comau and Leonardo Want to Elevate Aeronautical Structure Inspection with Cognitive Robotics
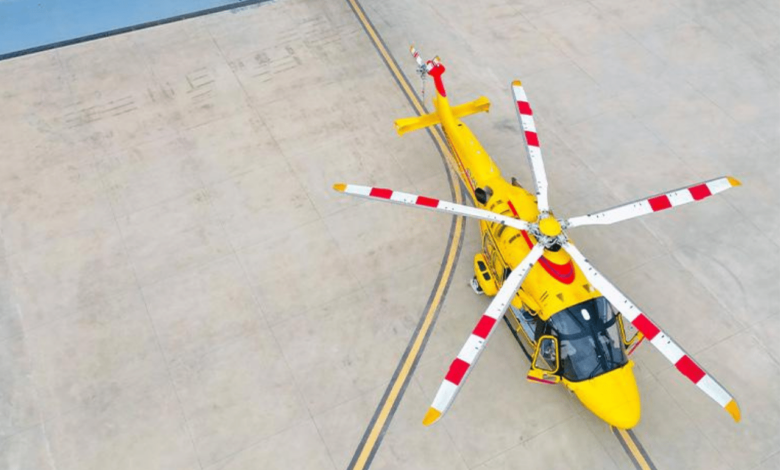
Robotic company Comau and aerospace company Leonardo are currently testing a self-adaptive robotic solution to enable autonomous inspection of helicopter blades. This could enhance quality inspections and offer greater flexibility without sacrificing precision or repeatability. At a time when the aerospace industry demands faster processes, better control, and higher quality, it requires a new generation of advanced automation. We contacted Simone Panicucci, Head of Cognitive Robotics at Comau to know more about this solution and how it could benefit the aerospace industry.
The increasing demand for faster processes in the aerospace industry requires to automate complex processes that, until recently, could only be manual. When it comes to testing essential structures such as helicopter blades, the potential benefits of automation increase exponentially. Robotic inspection ensures precision and efficiency. It also ensures standardization and full compliance with the testing process by objectively executing each assigned task.
To meet the industry’s needs, Comau and Leonardo have been testing an intelligent inspection solution based on Comau’s cognitive robotics, on-site in Anagni, Italy to inspect helicopter blades measuring up to 7 meters.
The solution relies on a combination of self-adaptive robotics, advanced vision systems, and artificial intelligence. Comau’s intelligent robot can autonomously perform hammer tests and multispectral surface inspections on the entire nonlinear blade to measure and verify structural integrity, with a granularity exceeding thousands of points.
The robot perceives and comprehends its environment, makes calculated decisions, and intuitively optimizes the entire inspection process.
They will then test the system on another site to enhance MRO (maintenance, repair, and overhaul) service capabilities.
We contacted Simone Panicucci, Head of Cognitive Robotics at Comau who gave us more details about this collaboration.
How did the collaboration between Comau and Leonardo come about?
Simone Panicucci: “The collaboration grew out of Leonardo’s need to ensure advanced autonomous inspection of highly critical aviation infrastructure using cognitive robotics. The two companies are collaborating to develop and test a powerful, self-adaptive robotic solution to autonomously inspect helicopter blades up to 7 meters in length. Aerospace is not a sector that is used to automation yet. The high variability and the low volumes act as constraints toward a deep automation adoption. Cognitive robotics solutions are thus a key enabler to provide the automation benefits (such as process engineering, repeatability, and traceability) even with heterogeneous products and unstructured environments and Comau is leading the creation of AI-based, custom robotic solutions.”
What are the main features of this robotic solution?
Simone Panicucci: “The solution developed is a self-adaptive and efficient machine to inspect really large helicopter blades. It includes a visual inspection as well as a tapping test. It consists in physically stimulating the blade surface with an ad-hoc little hammer to recognize from the consequent sound if there is any issue in the blade’s internal structure. Jointly, both inspections require testing tens of thousands of points on the overall blade.
The robot can sense the environment, and locate the blade in the space with an accuracy below 10 mm. It can also understand potential objects in the scene the robot may collide with. And it can calculate at run time the optimal and collision-free path planning to complete the task.”
How does Comau’s intelligent robot perceive the environment?
Simone Panicucci: “The solution is provided with a 3D camera whose input is elaborated by a vision system to merge multiple acquisitions, post-process the scene acquired, and then localize both the helicopter blade as well as potential obstacles.”
What decisions does it make autonomously during the inspection process?
Simone Panicucci: “All the movements performed by the robot are calculated once the scene has been sensed, which means that no robot movement has been offline calculated. Additional sensors have been added to the robot flange as an external and independent system to avoid damaging the blade.”
How does this solution differ from manual or traditional inspection methods?
Simone Panicucci: “Today, helicopter blade inspection is done manually. The provided solution offers greater accuracy and efficiency, ensuring standardization and full compliance with the testing process by objectively completing each assigned task. Operators now program the machine, codifying their experience through a simplified user interface. The machine can work for hours without intervention, providing an accurate report summarizing critical points at the end.”
How does it guarantee higher quality and greater flexibility without compromising accuracy or repeatability?
Simone Panicucci: “The flexibility is given by the fact that the solution is able to deal with different helicopter blade models and potentially even different helicopter components. In addition, accuracy and repeatability are typical automation takeaways, now even improved thanks to vision system adoption.
Increased quality is due to the fact that the operator can now focus on the activity where he/she brings most of the value, the defect detection and confirmation, instead of mechanically performing the inspection.”
Given the importance of aviation facilities, how do Comau and Leonardo ensure that each task assigned is carried out objectively and is compliant?
Simone Panicucci: “Operator knowledge is always at the center. Leonardo personnel keep the final word regarding the helicopter blade status certification as well as any point inspected. The automation solution aims to alleviate operators from the repetitive task of manually inspecting tens of thousands of points on the helicopter surface. After hours of signal recording, the solution generates a comprehensive report summarizing the results of AI-based anomaly detection. The industrialized solution ensures repeatability, reliability, and traceability, covering and accurately performing the task.”
How are safety and compliance guaranteed in the process?
Simone Panicucci: “The solution is CE-certified and incorporates both physical and virtual safety measures. Physical barriers and safety lasers create a secure perimeter, halting operations instantly in the event of unexpected human intrusion. Furthermore, the solution ensures safe loading and unloading of helicopter blades and verifies proper positioning by requiring operators to activate safety keys from a distance of approximately 10 meters.”
What specific advantages does this solution bring to the aerospace industry?
Simone Panicucci: “This solution demonstrates that product heterogeneity and low volumes, typical of the aerospace sector, no longer constrain automation adoption. Comau’s cognitive robotics approach enables the delivery of effectiveness, quality, and repeatability even in unstructured environments and with low volumes. It easily adapts to different helicopter models and blades. Executing a process like the tapping test necessitated defining requirements and process engineering. This involved defining the material of the tapping tool, as well as the angle and force to apply. Additionally, all labeled data, whether automatic or manual, are now tracked and recorded, facilitating the creation of an extensive knowledge base to train deep learning models.”
What are the prospects for this technology?
Simone Panicucci: “Leonardo has been conducting tests on this solution as part of a technology demonstration. This technology holds potential benefits for both Leonardo and its customers. It could standardize inspection processes globally and may be offered or deployed to customers with numerous helicopters requiring inspection.”
Do you think this approach to robotic inspection can be extended to other industrial sectors?
Simone Panicucci: “The specific solution could obviously be extended to other inspections in the helicopter sectors as well as the avionics. But it is worth mentioning that from the technology point of view, the software pipeline, as well as the localization and optimal path planning may be easily applicable in other inspection activities as well as manufacturing or even continuous processes, like welding.”
What are the next steps for the implementation of this solution?
Simone Panicucci: “The next steps involve thorough testing of the automation solution at another Leonardo Helicopters plant. This process will contribute to ongoing improvements in the knowledge base and, consequently, the deep learning algorithm for anomaly recognition.”