Elysium Robotics’ Artificial Muscles are Paving the Way for Humanoid Adoption
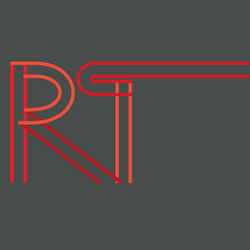
While adoption of single-purpose cobots is widespread in industrial settings, the potential of general-purpose humanoid robotics remains largely untapped, with their appeal being their versatility.
Elysium Robotics’ Artificial Muscles are Paving the Way for Humanoid Adoption
Elysium Robotics’ Artificial Muscles are Paving the Way for Humanoid Adoption
Mark Hammond & Rodrigo Alvarez-Icaza.Co-Founders | Elysium Robotics
Humanoid robots are ideal for automation of manual tasks. Yet, humanoids have thus far struggled to make it beyond the concept phase and a large gap exists between human capability and humanoid performance. While adoption of single-purpose cobots is widespread in industrial settings, the potential of general-purpose humanoid robotics remains largely untapped, with their appeal being their versatility.
“The bottleneck for the production of humanoids is in the actuators”. – Macquarie Research
Though motors and other current actuation technologies are sufficient for some motion needs, they have significant limitations for niche applications such as prosthetics and robotics, which may require a more compact and efficient source of motion production. Specifically, problems with previous actuation methods for such applications include high costs, heavyweight and bulkiness, inefficient battery use, and noisiness. We will not be able to deploy robots at scale without high-performance, low-cost actuators. The same actuation that facilitates dexterity for humanoids is also applicable to prosthetics.
“We believe hands, or more specifically grasping and manipulation, are the key pathway to applying real-world AI to the labor market, given that more than 98% of all work requires the dexterity of the human hand.” – Sanctuary.AI CEO
Dielectric elastomers resemble properties of human skeletal muscle
The quest for efficient, powerful and lightweight actuation technologies has recently focused on the use of dielectric elastomers for creating so-called “artificial muscles”. Dielectric elastomer actuators (DEAs) have for years been promising candidates for soft actuators and have commonly been referred to as artificial muscles since their emergence in the 1990s, primarily due to their elastic nature, activation by electricity, high actuation speeds, and high work densities, all resembling the properties of human skeletal muscles.
Dielectric elastomers in the shape of thin films have been heavily investigated, but do not produce beneficial strains and forces comparable to that of skeletal muscles without entailing extremely complicated fabrication processes, rendering their practical use limited. Ideally, the DEAs should be fiber-shaped to mimic the skeletal muscles truly and to enable novel structures, but fibers with the required dimensions and properties have not been easily achieved until now through Elysium.
Fig 2. Thin Film Dielectric Elastomers Fig 3. Fiber Shaped Dielectric Elastomers
Planar, unusable displacement Axial displacement can be harnessed
Elysium Robotics Intro:
Elysium Robotics develops artificial muscles that allow for low-cost, mass production of high-dexterity applications such as humanoid robots and prosthetics. No better actuator exists that can be used to produce a low-cost hand with human performance claims Mark Hammond, co-founder of Elysium. A 27 DOF hand can be built for under $1k using Elysium technology. A Shadow Robotics hand in comparison costs over $100k to purchase.
https://www.elysium-robotics.com/
Co-Founder: Mark Hammond
Co-Founder: Rodrigo Alvarez-Icaza
Elysium Robotics Product:
Elysium has created a soft robotic dielectric elastomer actuator that can be mass-produced at low cost with performance and footprint similar to human muscle. By applying a voltage across the fibers, tension can be modulated, and size and strength controlled, just like it is with human muscles. Elysium’s design does not require motors, gearboxes or other moving parts. Fibers are controlled through a voltage differential and are extremely precise and easy to control.
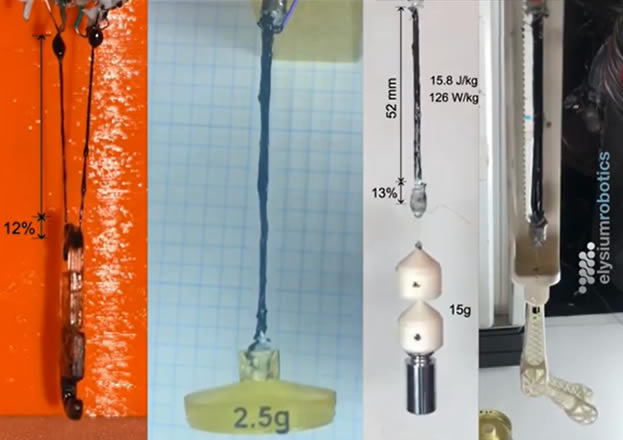
Link to fiber demonstration: https://www.youtube.com/watch?v=02FQVQjIPqA
When comparing actuator types, fiber form dielectric elastomers are the clear solution to achieving human level performance at a low cost.
Current Performance Characteristics:
● Customizable Sizes: Scalable from single fibers to thousands, 100 µm to m diameters
● Lightweight: 50% lighter than servomotor, >10 J/kg
● Better Form Factor: Motors are bulky and require transmissions. Elysium has a natural form factor comparable to human muscle
● Low Power and Low Thermal Footprint: Lower holding power then servos. 40% efficiency, no holding current
● Cost:<10% of a comparable servo
● Speed: 50 ms activation time
● Robust: Stretches without breaking
● Safety: Food grade and intrinsically compliant
● Accuracy: ><1% intrinsic hysteresis.
● Noise: 0 dB, no noise
● Manufacturable: Material abundance on and off planet (Mars)
● Strong: 150 kPa
● Speed: 50 ms activation time
● Reliable: >5M cycles
● Controllable: Smooth movement
The content & opinions in this article are the author’s and do not necessarily represent the views of RoboticsTomorrow
Comments (0)
This post does not have any comments. Be the first to leave a comment below.
Featured Product
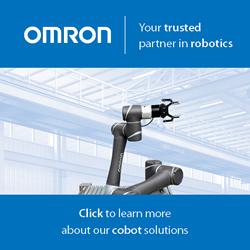
Discover how human-robot collaboration can take flexibility to new heights!
Humans and robots can now share tasks – and this new partnership is on the verge of revolutionizing the production line. Today’s drivers like data-driven services, decreasing product lifetimes and the need for product differentiation are putting flexibility paramount, and no technology is better suited to meet these needs than the Omron TM Series Collaborative Robot. With force feedback, collision detection technology and an intuitive, hand-guided teaching mechanism, the TM Series cobot is designed to work in immediate proximity to a human worker and is easier than ever to train on new tasks.