Enhancing EV Efficiency With Battery Purity
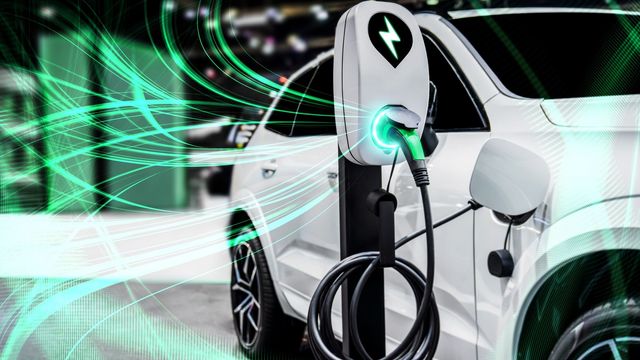
Thank you. Listen to this article using the player above. ✖
Electric vehicle battery performance is becoming ever more crucial as the EV market rapidly evolves. Changing tariffs and incentives for EV manufacturers and consumers, along with variable adoption rates of electric car ownership in different territories, are creating a more nuanced global ecosystem.
Sales of EVs are rising in markets such as the US and China but at a lower rate than at the turn of the decade. In Europe, rates for hybrid purchases are higher than for electric-only cars. As economic pressures increase, it is imperative that battery suppliers demonstrate their pivotal value to automakers or risk losing their market share to competitors.
From a commercial standpoint, lithium-ion batteries are still the preferred renewable power option for most car manufacturers, with energy capacity, fast charging, low discharge rate and lifespan being key factors. Battery producers must show how their units will positively impact the performance of a vehicle, and to do this, each of a battery’s four functional components – the cathode, anode, separator and electrolyte – has to be free of contaminants to operate at maximum efficiency.
Overcoming the complexity of cathode active materials
The formation of the cathode – the positive electrode – is the most complex process in EV battery manufacturing, and its composition can account for around 40% of the battery’s cost. This elemental part of the technology also significantly affects the battery’s performance. To allow the battery to operate at an optimal level, these materials must be as pure as possible. Contaminants diminish performance and so must be eliminated.
Cathode active materials (CAM) are typically composed of metal oxides that are ground and mixed into a water-based slurry and then coated onto an aluminum foil which is then compressed (known as “calendaring”), to create the cathode electrode. The most common cathode materials used in lithium-ion batteries include lithium cobalt oxide, lithium manganese oxide, lithium iron phosphate and lithium nickel manganese cobalt oxide.
Manufacturers of CAM face several challenges due to the presence of other chemicals and materials that need to be removed, and the requirement to meet specifications on particle size and levels of contaminants. They must also preserve the structure of crystals and control their surface area and porosity.
Filtering for purity
This is where high-performance filtration systems are needed to achieve the requisite levels of purity, removing undissolved salts, iron contaminants and larger particles from the precipitated mix at various stages in the process. A range of coarse metallic strainers, 0.3–5 µm depth filters and regenerable filters can be used to achieve liquid, chemical and gas purity levels that make the final cathode electrode more efficient and stable in operation.
Contamination in the CAM slurry mix will reduce the electrode’s effectiveness resulting in lower battery performance and shorter discharge life. With increased CAM purity, manufacturers can maximize performance but only if other complementary factors such as electrolyte cleanliness and polymeric separator materials are also of a high material standard.
The processes for creating the anode are similar but mix graphite with a binder (often polyvinylidene fluoride) and a solvent such as N-methyl-2-pyrrolidone. This anode slurry is coated onto a copper foil.
Minimizing corrosion from the electrolyte
Cleanliness of the electrolyte is necessary to facilitate the transfer of the ions between the anode and cathode. The solution of lithium salts and organic carbonates such as ethylene carbonate or dimethyl carbonate must be pure enough to enable ionic conductivity and chemical, electrochemical and thermal stability.
Controlling water content is also essential. Moisture in the electrolytes can result in hydrofluoric acid (HF) from fluoride lithium salts. As HF can corrode certain metals – such as those present in internal battery components – it is critical to prevent moisture from encountering the electrolytes.
Due to the high degree of acidity of the electrolyte, chemically-resistant filter materials and fluoropolymer-coated stainless steel filter vessels are recommended. Filters with fine particulate removal ratings (0.45–2 µm) are appropriate to achieve high levels of electrolyte cleanliness.
Quality control to optimize performance
Batteries require separators to prevent short circuits and ensure safe operation. There are several steps involved in producing them, with challenges to be met to ensure cleanliness, uniformity, robustness and porosity for ion transportation. To achieve quality control, manufacturers must consider homogeneity and purity of raw materials such as plasticines and additives, temperature and thickness control and constancy of speed of production.
Polymer melt filter technology ensures chemical companies can supply high-quality polymeric separators to EV battery manufacturers. Purification steps include filtration of the molten polymer before film formation and filtration of various other additives and coatings used in the process.
As demand for lithium-ion batteries increases to meet the needs of a projected growth in the EV market, suppliers must reinforce their critical role in the value chain. The performance, range and durability of a vehicle depend on the efficiency of the battery. It is absolutely essential, therefore, to ensure the purity of a battery’s materials in order to generate optimal EV performance.
About the author:
Anoop Suvarna is the global battery materials manager for energy storage at Pall Corporation. He has more than 20 years’ experience in energy and industrial sectors and has a BA in Industrial Chemistry from Somaiya Vidyavihar University in Mumbai, India.