Enhancing Industrial Robot Performance Through Time-Lag Filtering
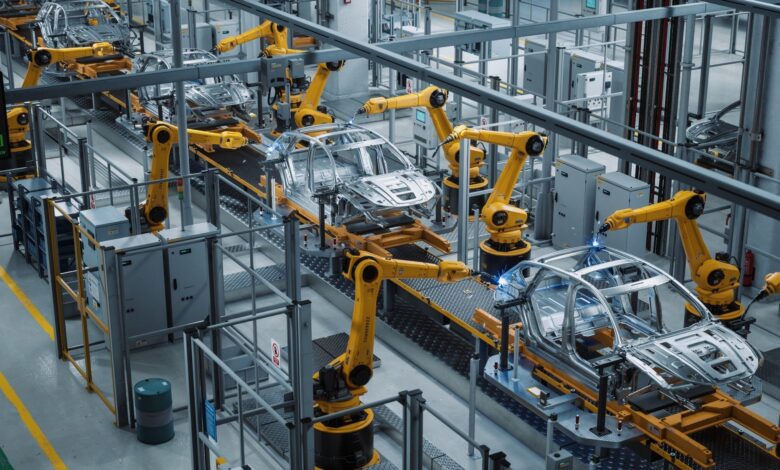
In a recent paper published in the journal Machines, researchers from China proposed a novel method for reducing vibrations in industrial robots through time-lag filtering based on trapezoidal trajectory (T-trajectory) interpolation. Their technique targets enhancing the accuracy and stability of robot motion by reducing the amplitude of harmonic components within specific frequency bands.
Additionally, they conducted a comparison of this approach with other vibration suppression methods, including closed-loop control-based dynamic feedforward, showcasing its effectiveness in terms of accuracy, real-time performance, and cost.
Background
Industrial robots are extensively utilized in manufacturing due to their high productivity, cost-effectiveness, and safety features. However, a significant challenge in robot control is the presence of vibrations, which can adversely impact the robot’s performance, work stability, product quality, and durability. Vibrations can be caused by various factors, including the structural flexibility of the robot, the joint drive system, load variations, resonance frequency, changes in mechanical structure rigidity, and high-speed motion. These vibrations can lead to positional deviations of the robot’s end-effector, instability, increased mechanical component wear and tear, diminished product quality, and compromised worker safety. Therefore, vibration suppression emerges as a critical area in industrial robotics research.
Traditional methods for suppressing vibration in industrial robots include mechanical design, control systems, and material selection. These techniques aim to reduce or eliminate vibration by enhancing the rigidity of the robot structure, incorporating damping materials or shock absorbers, employing sensors and feedback controllers, implementing predictive or adaptive control algorithms, integrating active vibration suppression devices, and optimizing control inputs and trajectories. However, these methods may encounter challenges related to accuracy, real-time performance, and cost.
About the Research
In this study, the authors introduced an innovative technique for effectively suppressing vibration in industrial robots based on time-lag filtering with T-trajectory interpolation. They selected a frequency band according to the robot body’s vibration characteristics and designed a related time-lag filter. The filtered trajectory could decrease vibration amplitude, potentially minimizing vibration to zero under ideal conditions.
The time-lag filtering technique is especially suitable for incorporation into the trajectory planning component of a robot controller. This approach can directly improve performance via software algorithms, without modifying the controller’s overall hardware and software architecture. The principle of time-lag filtering involves using a finite impulse response (FIR) filter to shape the input signal and suppress the harmonic components in a specific frequency band.
Additionally, the researchers presented a method for T-trajectory interpolation, a technique aimed at ensuring accurate, smooth, and efficient motion execution when a robot follows a T-trajectory. T-trajectory interpolation involves using a smooth curve to generate the robot’s position, velocity, and acceleration at each moment, thereby avoiding robot instability during path switching. This technique inserts additional points in the robot’s path to achieve the required motion.
The proposed technique combines the time-lag filtering method with the T-trajectory interpolation method to dynamically adjust the trajectory output and reduce the vibration amplitude of the robot. Moreover, the study introduces a straight-line method to measure the degree of vibration and compares the proposed method with other traditional methods through experiments.
Furthermore, the authors conducted experiments on a SIASUN 20 kg flexible robot (SIASUN, Shenyang, China) to test the effectiveness of the proposed method in suppressing vibration. They utilized a dynamic signal test analyzer, a laser tracker, and a micrometer to measure the robot’s vibration trajectory, accuracy, and stability. Additionally, they compared the proposed method with two other methods: one based on closed-loop control of feedforward dynamics and the other based on predictive control. The study also introduced a new concept of “average amplitude ratio” (AAR) as a measure of the vibration suppression effect.
Research Findings
The outcomes showed that the proposed technique significantly reduced the vibration of the industrial robot and improved its motion accuracy and stability. It decreased the AAR of vibration from 0.841 and 0.498 to 0.306 compared to classical methods, indicating a more effective vibration suppression effect. The authors emphasized that the proposed method enhanced the robot’s vibration performance. It also improved the robot’s straightness, demonstrating its ability to maintain trajectory planning, achieving a straightness of 0.001 mm compared to the dynamic feedforward method’s 0.005 mm.
Moreover, the novel method can be applied to various industrial robot applications requiring high precision and efficiency, such as drilling, milling, welding, and assembly. By enhancing robot performance and reliability, it can meet the growing demands of modern manufacturing. Additionally, the method can offer valuable insights into vibration issues across different fields, fostering interdisciplinary application and technological advancement.
Conclusion
In summary, the introduced method efficiently reduced the vibration of industrial robots and enhanced their reliability and accuracy in task performance. It effectively addressed the demand for precision and efficiency in modern manufacturing, improving overall robot performance.
However, the researchers acknowledged several limitations and challenges, including the delay induced by time-lag filtering and the optimization of filter parameters. Moving forward, they proposed directions to enhance and expand their methods, such as applying them to different robotic systems and various application scenarios.
Journal Reference
Liu, S.; Wu, C.; Liang, L.; Zhao, B.; Sun, R. Research on Vibration Suppression Methods for Industrial Robot Time-Lag Filtering. Machines 2024, 12, 250. https://doi.org/10.3390/machines12040250, https://www.mdpi.com/2075-1702/12/4/250.