Forget the Hype – Here’s Some Real AI
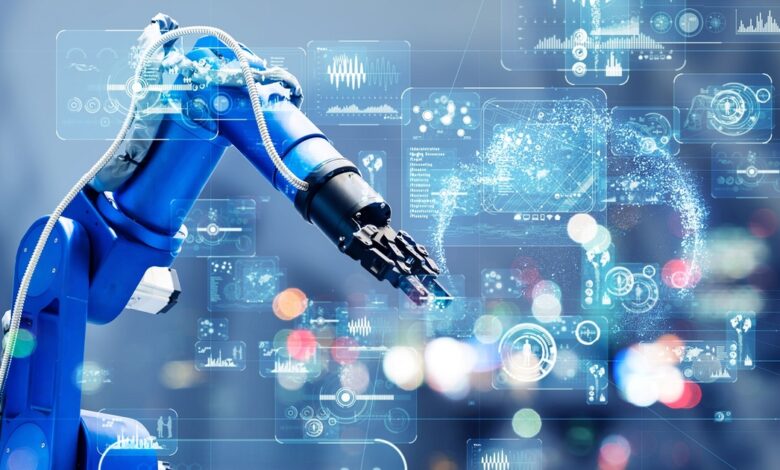
We are constantly hearing about AI, especially in the area of industrial systems. But what is actually happening in the real world? Industrial AI is often viewed as a fusion of artificial intelligence and industrial technologies. The combination is revamping manufacturing and production processes. The notion is that if you integrate AI algorithms with industrial machinery and systems, you’ll get optimized efficiency, productivity, and safety in manufacturing environments. Sounds great. But what’s really happening?
Delta Bravo founder and CEO Rick Oppedisano is offering a behind-the-scenes look at industrial AI solutions, using his experience with Nucor Steel, Rolls-Royce and more. He will share the “Holy Grail” of datasets used as the foundation for successful equipment reliability, quality and supply chains during his keynote talk Industrial AI: Cut Through the Hype and Get Real at IME South in Charlotte, N.C. on Tuesday, June 4 at 2:00 PM. IME South, which features six different co-located shows: Design & Manufacturing South, ATX South, MD&M South, SouthPack, Plastic South, and Powder/Bulk Solids South.
Oppedisano will discuss the some of the success stories of Industrial AI Copilots and explain why some AI projects have failed. He will share Delta Bravo’s AI Value Framework, which is used to identify, score, and prioritize use cases with over 90 industry leaders since 2016.
Here’s an Epicore podcast with Oppedisano explaining what manufacturing will be like in the future.
We caught up with Oppedisano to get his view of industrial AI, its promises, its successes, and its failures.
What products in the market are already using AI?
Rick Oppedisano: AI is not new. A lot of AI products has been enterprise ready for some time. One is computer vision software. The software detects anomalies and detects defects. Large amounts of data sets evaluate products that are scanned. The vision software uses a model that changes over time.
Is predictive maintenance is a form of AI?
Rick Oppedisano: In predictive maintenance has been glorified because it alerts users that a threshold has been broken. What has been used in the market is single variant forecasting. It’s just one variable. That’s helpful, but it doesn’t tell you why it’s happening. We use vision software to bring data in from different sources. We then do multiple quality checks. We access ERP data and put it together to get an understanding of what correlates to this problem. Are we stressing out the machine, are we seeing drift? Now, everyone and their mother says they’re AI. Most of what’s called AI is single-variant analysis, something a child can do.
Explain how your use AI
Rick Oppedisano: Secret sauce for us is working with people who don’t know the first principle of solving the problem. How do I solve a process problem that reduces risk and improves my efficiency? They don’t want to add more duties to a process they’re already struggling to do. Manufacturers are trying not to disturb the process because it’s their business.
The number-one problem fo manufacturers is people. The average tenure of a worker in 2019 was 20 years. Now it’s 3 years. That means quality problems will be rooted in inexperienced people. You also have a disconnect between how my generation learned and how young people are learning now. They expect answers to be on a screen. So, we take data from all through the process and show them why things are happening instead of waiting to something to go wrong. Real-time feedback help helps the young inexperienced workers do a better job. It’s through an interface they can understand.
How is AI helping with these challenges?
Rick Oppedisano: The checkmate thing is people. Those who run manufacturing are afraid of AI solutions because they don’t want to disturb their operation. Yet they have to reconcile the inexperienced worker situation. What we’re doing is taking data from different parts of the operation and creating a data set. We create a demand forecast that matches the plant’s operation. We use that data to go back to the inventory and adjust it dynamically. It’s all connected. It’s an ecosystem. If you kill algae on one side of the pond it will affect fish on the other side.
The models we create can become the brain for the manufacturing system. There is going to be a progression to the brain that can help do tasks with greater understanding. My dad was in manufacturing. The reason I started this company was to restore US manufacturing. Manufacturers see that what they do affects the country positively. Restoring manufacturing is a big problem, and we’re taking a big swing.