Generative AI assists field personnel
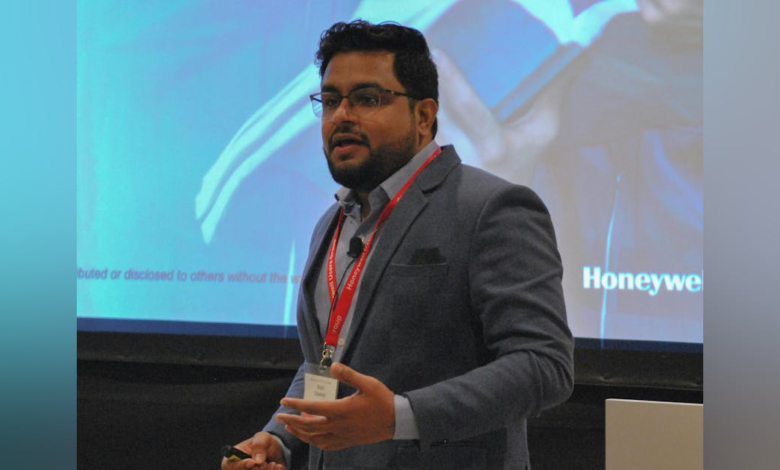
Say adios to manual, paper-based systems that can be a black hole for field personnel’s time. “A field tech can carry 50-70 pages of documentation,” said Hrishikesh Upasani, Honeywell’s offering manager, workforce excellence. A more efficient option, he suggested, would be to ask generative artificial intelligence (AI) for the information or answer you need.
Announcing the launch of Field PKS at the Honeywell Users Group meeting this week in Madrid, Upasani presented use cases that ask AI to retrieve a P&ID or job tags, perhaps even access spare-inventory data. “With Field PKS, everything is available,” explained Upasani, “even if your network is not working. The field tech should be able to access information in off-line mode.”
With a summer 2024 launch ahead, pilot users can still join and help to direct the development of new features, as well as benefit commercially, said Upasani. The initial product will connect with a company’s SAP enterprise resource planning (ERP) system for work orders, maintenance records and inventory of spares. Plans for connectivity with other ERP systems are in the works. Likewise, connectivity to Experion PKS for real-time and historical data, as well as alarming and trending, is available with the initial launch, while connectivity to other distributed control systems is a possibility for the future.
Equally important is the Field PKS platform’s access to document repositories for OEM documentation, plant-specific procedures and safety guidelines, as well as access to OT systems for operations management, asset performance management and alarming management.
Field PKS will feature two interfaces—one for supervisors and planners and another for field operators and technicians. The supervisor screen display will include a dashboard for job-pack creation, analytics and reporting, while the field worker’s handheld, Android/iOS-based mobile display will give access to the generative-AI-based assistant, powered by ChatGPT 4.0, which can provide a variety of contextual information.
Connecting the dots
Field technicians and their supervisors face a variety of challenges due to disparate systems that have been siloed for decades. Field PKS looks to address those by using generative-AI technology to bridge those silos and make informed decisions based on specific application needs.
Despite overwhelming access to data, many organizations still look to gain better insights into that data. And, with the loss of skilled and experienced staff to retirement and turnover, tribal knowledge is being lost. Field workers are being asked to complete tasks right the first time, despite data that’s often asymmetrical between the field and the SAP panel, said Upasani, whose development team identified multiple challenges—operations-to-maintenance handovers; unavailability of contextual data in field; equipment location identification; frequent reskilling/upskilling needs; field collaboration; history capture; resource allocation; and safety concerns—that Field PKS addresses.
The initial vision is to interface with the ERP, document system and visual communication system, as well as Honeywell’s Experion PKS, historian, asset performance management software, field device manager and operations management software.
“We need to have a one-stop shop for our customers who do all of their work in the field,” explained Upasani. “We need to make use of cutting-edge technology such as generative AI and artificial reality to provide complete visibility of field and workflow management. Field PKS is a rich, web-based application for faster scheduling and tracking of planned and unplanned maintenance.”
For maintenance personnel, Field PKS integrates the ERP system for work orders, past maintenance records and spares inventory, as well as related documentation from the Experion PKS or other systems. The supervisor gets a dashboard to monitor and manage tasks, personnel and inventory.
Upasani presented a use case involving a split case pump, which typically has its axial wear rings replaced every 5,000 running hours. There are five steps and five separate pieces of documentation for that process, which normally takes 36 hours to perform, he said. The generative-AI assistance of Field PKS is able to turn that into a 20-hour process, saving 16 hours, as well as an additional $12,000 savings in spare-parts consumption.
Using Field PKS reduces human error, downtime, maintenance expense, direct material expense and working capital, explained Upasani, who shared a plethora of calculated benefits for users, including an 80% reduction in time spent on procedure preparation, a 20% decrease in wrench time and a 25% decrease in equipment downtime, not to mention decreases in insurance costs.