Harvestance – Developing and Designing Vacuum Grippers for Production Line Robots
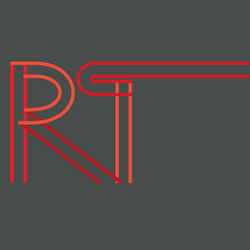
Harvestance, a design and engineering services company, specializes in additive manufacturing. They provide 3D printing design solutions (DfAM) and services across various industries, including automotive, semiconductors, footwear and food tech. Harvestance has received numerous inquiries for the design and manufacture of customized, lightweight, and strong grippers for collaborative robots, aimed at automating production lines.
Traditional aluminum grippers, often heavy, limit the weight of workpieces that can be lifted and consume more energy. Harvestance’s customers, including collaborative robot users and robot system integrators, expressed several pain points:
“We were convinced that 3D printing could fully address these pain points. We chose Markforged composite 3D printing technology to reduce the gripper’s weight while improving its strength and stiffness, optimizing performance,” explains Harvestance CEO Seungjae Leem.
Harvestance focused first on lightweight design, integrating vacuum channels from the compressed air source to the suction cups directly into the gripper body, enabling one-touch fitting without external tubes. They adopted various design methodologies to enhance the quality and efficiency of 3D printed parts, such as redesigning to minimize surface roughness and creating self-supporting internal vacuum channels. This approach improved quality and reduced time and costs.
Part material is critical for factory production tools like grippers. Mr. Leem and his engineering team tested various printers and materials including Fused Filament Fabrication (FFF), Stereolithography (SLA), Selective Laser Sintering (SLS), and Powder Bed Fusion (PBF). Only Markforged, with Onyx and Carbon Fiber Reinforcement, could meet the flexural and impact strength these parts required for certification.
Another Markforged advantage is superior surface quality. All of the other 3D printers Harvestance evaluated required post processing steps, such as melting away support structures, depowdering, washing and curing, or polishing. But Markforged printed parts come off the print bed ready to use, without any delay or extra labor cost for post processing.
“
We chose Markforged composite 3D printing technology to reduce the gripper’s weight while improving its strength and stiffness, optimizing performance.”
– Seungjae Leem CEO of Harvestance
Harvestance turns to the Markforged FX20 when they need to print larger tools such as customized grippers for palletizing and heavy pick and carry tools for large industrial robots. The faster FX20 also speeds up production 3 to 4 fold.
“Utilizing Markforged 3D printing technology, we achieved an 80% weight reduction compared to standard commercial grippers and reduced delivery time from two weeks to two days, compared to conventional CNC machined grippers,” says Harvestance CEO Seungjae Leem.
By reinforcing the bottom of the gripper body with continuous carbon fiber and glass fiber, Harvestance created a strong, light gripper capable of supporting heavy workpieces without altering its shape.
“Markforged’s high-strength material (Onyx), Continuous Fiber Reinforcement, excellent surface finish, and easy post-processing have been ideal solutions for us. Our engineers can focus entirely on their work, developing products without concerns about mechanical properties, post-processing burden, or quality,” added Leem.
“
Utilizing Markforged 3D printing technology, we achieved an 80% weight reduction compared to commercial grippers and reduced delivery time from two weeks to two days, compared to conventional CNC machined gripper.”
– Seungjae Leem CEO of Harvestance
The Future
Harvestance is harnessing its mechanical design capabilities and DfAM solutions, along with Markforged composite 3D printing technology, to develop and launch a brand of lightweight, strong, customized, and affordable grippers.
They are currently providing robot gripper services tailored to individual customer needs. Their ultimate goal is to offer a service that quickly supplies parts customized to each customer’s conditions, regardless of time and place. As a first step, they developed an algorithm for automatically designing customized grippers and are building an online platform for customers to design, order, and pay for these grippers. This initiative will soon expand to include items like finger grippers and gripper tips.
In addition to design automation, Harvestance aims to automate production systems by leveraging the Markforged Digital Forge platform for parts ordered through their online 3D printing service platform.
“
Markforged’s technology and the easy production process have been crucial in starting and expanding our robot End-Of-Arm Tooling business. We believe that the Digital Forge platform will enable us to further streamline and modernize our operations in the future.”
– Seungjae Leem CEO of Harvestance