Heat trick helps tiny robots grab, hold with 3D-printed muscle power
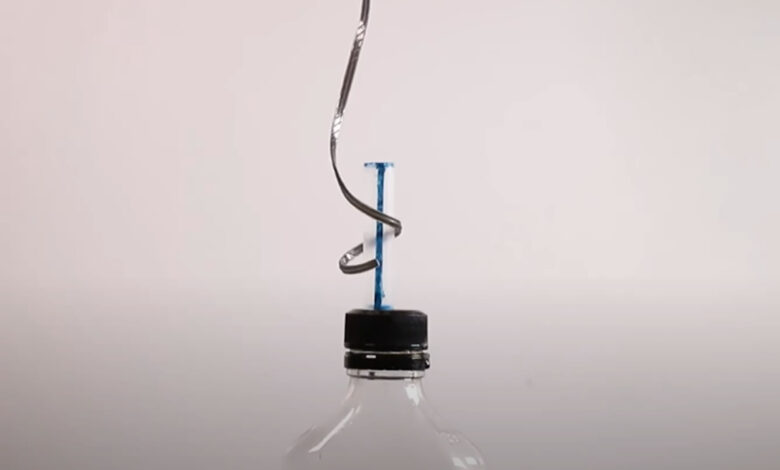
A team of researchers from North Carolina State University have developed a novel kind of soft-bodied robot that can be 3D-printed. The robots operate like soft hydraulic actuators and are less than a millimeter thick.
The robots’ design enables them to be deformed and controllable while also demonstrating shape memory. This combination enables the robots to mold into many shapes and return to their “neutral” form repeatedly and rapidly.
“Soft robotics holds promise for many applications, but it is challenging to design the actuators that drive the motion of soft robots on a small scale,” says Jie Yin, corresponding author of a paper on the work and an associate professor of mechanical and aerospace engineering at NC State.
He added that their approach utilizes commercially available multi-material 3D printing technologies and shape memory polymers to create microscale soft actuators, enabling them to control very small soft robots with exceptional control and delicacy.
3D-printable, soft-bodied robots
The new technique involves creating soft robots with two layers. The first layer is a flexible polymer made using 3D printing and contains microfluidic channels – tiny tubes within the material.
The second layer is made of a flexible “shape memory” polymer. In total, the soft robot is just 0.8 millimeters thick. Users can control the movement and shape changes of the soft robot by pumping fluid into the microfluidic channels, which creates hydraulic pressure.
According to the researchers, the pattern of the microfluidic channels dictates the robot’s motion and shape changes, such as bending and twisting. The speed and volume of the fluid pumped into the channels determine how quickly the robot moves and the amount of force it exerts.
If users want to ‘freeze’ the soft robot’s shape, they can apply moderate heat (64°C, or 147°F) and then let the robot cool briefly. This prevents the soft robot from reverting to its original shape, even after the liquid in the microfluidic channels is pumped out.
If users want to return the soft robot to its original shape, they simply apply the heat again after pumping out the liquid, and the robot relaxes to its original configuration.
“A key factor here is fine-tuning the thickness of the shape memory layer relative to the layer that contains the microfluidic channels,” says Yinding Chi, co-lead author of the paper and a former Ph.D. student at NC State.
“You need the shape memory layer to be thin enough to bend when the actuator’s pressure is applied, but thick enough to get the soft robot to retain its shape even after the pressure is removed,” he added.
The robots can grip things
The researchers demonstrated a technique by creating a soft robot gripper to pick up small objects. They used hydraulic pressure to make the gripper close around an object.
Then, they applied heat to keep the gripper closed even after releasing the pressure. This allowed the gripper to move with the object to a new position. When they applied heat again, the gripper released the object.
“This paper serves as a proof-of-concept for this new technique, and we’re excited about potential applications for this class of miniature soft actuators in small-scale soft robots, shape-shifting machines, and biomedical engineering,” Qing concluded.
ABOUT THE EDITOR
Christopher McFadden Christopher graduated from Cardiff University in 2004 with a Masters Degree in Geology. Since then, he has worked exclusively within the Built Environment, Occupational Health and Safety and Environmental Consultancy industries. He is a qualified and accredited Energy Consultant, Green Deal Assessor and Practitioner member of IEMA. Chris’s main interests range from Science and Engineering, Military and Ancient History to Politics and Philosophy.