Honda Begins Producing Fuel Cell Electric Vehicle
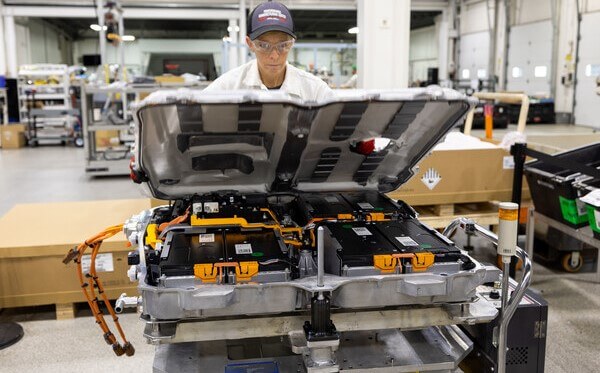
Honda is celebrating the start of production of the all-new 2025 Honda CR-V e:FCEV fuel cell electric vehicle (FCEV) at the Performance Manufacturing Center (PMC) in Ohio.
The all-new CR-V e:FCEV is the only FCEV made in America, as well as the first production hydrogen FCEV in the United States to combine an all-new U.S.-made fuel cell system with plug-in EV charging capability.
A fun-to-drive compact CUV, the CR-V e:FCEV received a 270-mile EPA driving range rating, combining the fuel cell system with plug-in charging to provide up to 29 miles of EV driving around town with the flexibility of fast hydrogen refueling for longer trips.
“The Performance Manufacturing Center was conceived as a small volume manufacturing facility with a focus on craftsmanship, and I’m proud of how our production technicians leveraged their experience building the Acura NSX to take on the challenge of making this all-new Honda CR-V e:FCEV,” says Patrick McIntyre, head of PMC. “Producing a zero-emission fuel cell electric vehicle is one more step toward Honda’s global goal of achieving carbon neutrality for our products and operations.”
The fuel cell system that powers the Honda CR-V e:FCEV is also made in the U.S. at Fuel Cell System Manufacturing LLC, in Brownstown, Michigan — the joint venture production facility established by Honda and General Motors (GM). This fuel cell system was co-developed by Honda and GM, achieving higher efficiency and increased refinement, with durability performance doubled and cost reduced by two-thirds compared with the previous fuel cell system in the Honda Clarity Fuel Cell.
Production technicians at PMC navigated several challenges related to new production equipment and processes to effectively transition from building the Acura NSX supercar to the Honda CR-V e:FCEV. These key initiatives include:
- New components. PMC technicians are taking on multiple new assembly processes specific to producing a vehicle powered by both a fuel cell system and a plug-in EV battery, requiring multiple connections for the vehicle’s two power sources and the Power Supply Connector that can provide electrical power for various external devices. These include:
- Subassembly of two hydrogen tanks, attaching high-pressure piping and other parts and then installing the tanks in the vehicle
- Compressing hydrogen to 10,000 PSI via a new onsite station used to fill the CR-V e:FCEV hydrogen fuel tanks
- Installation of the fuel-cell system along with connecting high-pressure piping and wiring
- Subassembly and installation of the under-floor battery
- New weld system. Transitioning to the CR-V e:FCEV required a complete transformation of the Weld Department, from a highly automated welding system created for an aluminum spaceframe to a multi-material unibody construction.
- The previous robotic weld system was removed and replaced with new steel welding robots that were installed with characteristics of a traditional weld system but are unique from mass production plants with a flexible fixture system that rolls around on a track.
- PMC technicians also now perform some manual MIG welding to apply welds that are difficult for robots to reach to attach closure parts for the doors, hood and tailgate.
- Paint system modifications. The larger and heavier all-steel body of the CR-V e:FCEV requires a different corrosion protection application process than the smaller, all-aluminum Acura NSX.
- The CR-V e:FCEV marks the first application in Honda North America of zirconium to a mixed metal, unibody, and utilizes the same high-appearance paint coating as the NSX. The E-coat dip tank was designed for the smaller surface area of the NSX spaceframe, not a full frame vehicle like CR-V with more surface area inside. So engineers had to modify the dip tank to enable the CUV body shape to enter at a 38-degree angle, steeper than the 15-degree angle for NSX. More precise control of the E-coat pumps also was required for CR-V, to create higher circulation of the E-coat to cover the surface area inside the frame.
- Following e-coating, but before application of the final paint finish, sealer is applied to prevent water leaks. The CR-V body is mounted on a rotisserie, but unlike the previous equipment arm used to turn the lighter NSX spaceframe, a more robust arm that can maintain stability of the heavier CR-V steel frame is used to turn the frame on its side. This enables associates to manually apply sealer similar to the application for the NSX.
Production of the FCEV at the PMC also is laying the groundwork for production of battery electric vehicles at the Honda EV Hub in Ohio from the standpoint of software for the Integrated Power Unit (IPU).