How robots are changing surgery
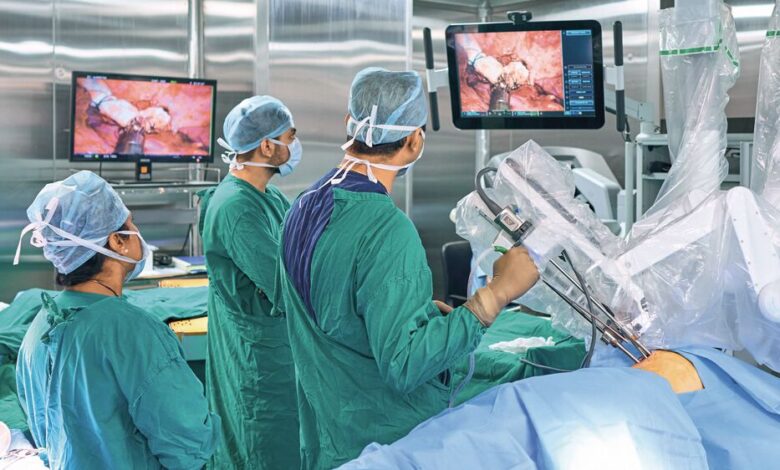
Persistent and connected
How robots are changing surgery
A guest post by
Klemens Thaler* | Translated by AI
A faster operation, shorter anesthesia times, and rapid recovery: the use of robotics in surgery offers advantages. However, the technology behind it is complex and users need to familiarize themselves with the legal basis.
(Image: © Alexander Lupin – stock.adobe.com)
Dr. Klemens M. Thaler is Group Leader at TÜV SÜD.
Robots don’t tire, their gripping arms don’t start shaking even after hours of use. But stamina is just one of their advantages in the operating room. Robot-controlled scalpels can make the smallest and finest cuts, optimizing minimally invasive operations. Patients thus recover faster. Cameras transmit real-time three-dimensional images of the procedure that can be magnified multiple times. The use of this innovative technology makes it possible to shorten operation times and thus the duration of anesthesia.
A robot system consists of the patient cart, a computer tower, and the surgeon console. Because robots do not work autonomously, but support the work of experienced surgeons. These sit at the console—possibly even several meters away from the operating table—and control the individual instruments. In doing so, they can adopt a relaxed posture, instead of having to bend over the operating table for long periods.
Medical robots have a lot of finesse: When the surgeon moves his hand a centimeter on the control, the robot can turn this into a cut of only a millimeter on the patient. Motors with low speeds and moderate torque allow precise control of the robot arms even at low speeds.
The human-machine interface is complex
The collaboration is mutual: robots transmit not only patient data to the surgeon, but also details of the surgical procedure, such as the resistance of the skin or tissue. The surgeon can then adjust the force he applies to the scalpel interface accordingly. The computer-assisted system simulates the haptic sensation of a real hand movement with a real scalpel.
The robot depends on receiving the right commands. Because the programming and design of the human-to-machine interface are complex, the users need to be trained accordingly. To be allowed to operate with robot assistance, comprehensive training is required, which also includes simulation training and residencies with experienced surgeons. The scope of the training is determined by the manufacturers and can include up to 250 training units. Even experienced surgeons need months or even years to master the new technology.
The technical progress of medical technology has overtaken legislation. Nevertheless, it is by no means a legally free space: For manufacturers and developers, the Medical Device Regulation (MDR) of the European Union is mandatory. It defines requirements for the performance and safety of robots in medical use. For robots for invasive procedures, the IEC 80601-2-77 of the International Electrotechnical Commission (IEC) comes into play. This international standard for robot-assisted surgery systems formulates requirements for the maximum permissible risks, such as motion control. The robot must implement the movements of the operator in the correct direction and at the right speed.
Safety thanks to the IEC standard 80601-2-77
In addition, the IEC standard stipulates that the system must trigger preventive stops, for example, if the camera’s view of the operating area is obstructed. All instruments then immediately remain in their current position. If there are complications or technical disturbances, an emergency stop is initiated: all processes of the robot system come to a standstill. The requirements serve the safety and integrity of the patients.
The same guideline also defines that medical personnel must be trained in the use of the technology. Because an unacceptable risk would be that the information from the human to the machine is transmitted incorrectly. Therefore, TÜV Süd offers courses for people who work with robots in the medical environment. TÜV Süd also provides further training for manufacturers, for example, on security against data loss or hacker attacks.
Typical applications for robot-assisted operations
In the daily routine of clinics, medical robots already significantly relieve surgeons today. Because they improve the quality of procedures, patients also benefit. Typical applications for robot-assisted operations are neurosurgery, procedures in internal medicine and urology. Another area of application is still underdeveloped: tele-surgery. Here, the surgeon sits at one location, the patient is at another—possibly thousands of kilometers away. The surgeon remotely controls the operating robot.
Specialists for difficult cases no longer have to be flown in, the operation can take place promptly. This allows procedures to take place in places that have so far been poorly served medically, such as in developing countries. So far, the application in telemedicine is still rare. However, the more rapidly the digitalization and technologization of medicine progresses, the more likely such operations will become in the future. (heh)
Detect errors in the lab already
For manufacturers and developers, the experts check whether all requirements of the robot systems for information security and technology have been met, including technical documentation, risk management, and cybersecurity. In addition, TÜV SÜD/Germany has a test laboratory: errors can be simulated here and it can be tested how resilient the robots are under extreme conditions. An early bird assessment can be booked during product development to avoid expensive corrections afterwards. The manufacturers receive comprehensive feedback, so that the experience from the laboratory can flow into product development.