Mass Production of New All-electric Explorer Starts at Ford’s EV Plant in Germany
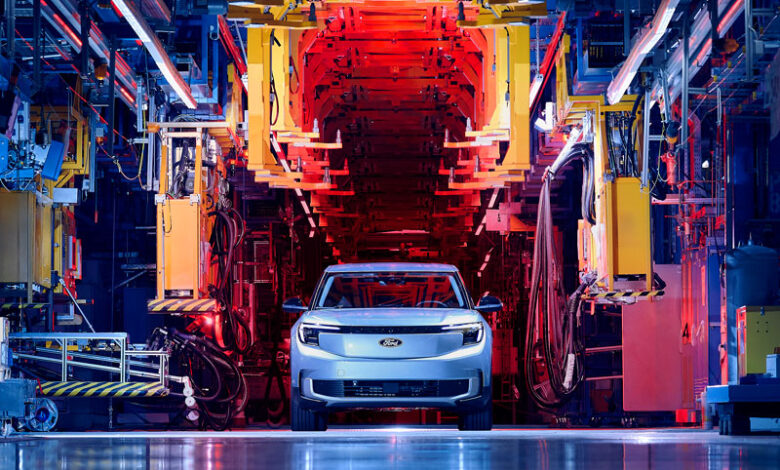
Ford Motor Co. in Dearborn has started mass production of the new all-electric Ford Explorer at its first dedicated electric vehicle facility in Europe.
Production at the Cologne, Germany plant follows a $2 billion investment that has transformed a historic plant into what the automaker calls “a factory of the future.”
The electric Ford Explorer is the first vehicle to roll off the line at the Ford Cologne Electric Vehicle Center — a step on the road to producing a new generation of electric passenger vehicles for the region. A second EV, a new sports crossover, will be revealed shortly with production in Cologne starting later this year.
According to Ford, the new Explorer EV combines German engineering, American attitude, and “superior” standard specification that includes battery electric powertrains for zero-tailpipe emissions while driving and more than 370 miles (600 km) driving range on a single charge.
“To see the Cologne factory founded by Ford in 1930 being transformed into a state-of-the-art electric vehicle production facility is nothing short of amazing,” says Kieran Cahill, vice president of manufacturing at Ford in Europe and International Markets Group.The start of mass production of electric vehicles, with the new all-electric Explorer, marks the beginning of a new era for Ford in Europe,”
The Cologne Electric Vehicle Center is equipped with cutting-edge AI and hundreds of carefully choreographed state-of-the-art robots that will deliver a “new generation of high quality EVs to Ford customers in Europe.” The plant’s “digital twin” monitors and supports production line operators to deliver high quality standards.
The Cologne Electric Vehicle Center is supported by self-learning machines and more than 600 new robots that execute welding, cutting, dusting, painting, and fusing tasks.
A new control center monitors the entire assembly process in real time — right down to the quantity of every part and nut at each workstation. The plant’s “digital twin” is displayed via a giant touchscreen containing all workstations with information on tooling, material delivery, work safety and more. With small touchscreens employees on the line provide further information on the status of their workplace.
“By monitoring and controlling every step of the manufacturing process, Ford will achieve unprecedented levels of quality for our customers,” says Rene Wolf, managing director of manufacturing for Ford-Werke GmbH.
The renovated plant is said to be one of Ford’s most efficient vehicle assembly plants globally, supported by reductions in emissions, water usage, and energy consumption.
The automaker says it’s working toward implementing a carbon neutrality pathway for the Cologne Electric Vehicle Center. With production now underway, greenhouse gas emissions data will be monitored and recorded for independent certification according to the latest international standards. Within this carbon neutrality pathway, Ford expects to continuously improve carbon efficiency and reduce GHG emissions toward a residual level.
In addition to initiatives that reduce emissions, water usage, and energy consumption, all electricity and natural gas required to operate the plant is 100 percent certified renewable electricity and biomethane. Ford is targeting carbon neutrality across its European production footprint of facilities, logistics, and direct suppliers by 2035.