New partnership proving high variability no obstacle to rapid automation
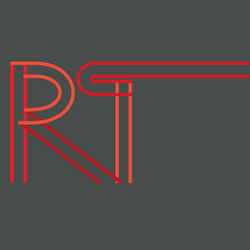
A new partnership between an industrial parts manufacturer and a VR robotics company is proving that high levels of variability are no obstacle to achieving rapid automation of production.
A new partnership between an industrial parts manufacturer and a VR robotics company is proving that high levels of variability are no obstacle to achieving rapid automation of production.
Founded in 2019 by Dr Chang Liu, Extend Robotics combines consumer Virtual Reality (VR) technology like Oculus and SteamVR, with artificial intelligence and robotics technology to make it easier for individuals to control robotics hardware remotely. The company’s aim is to make it easier for people and machines to work together in perfect harmony.
The robotics company’s latest partnership with industrial parts manufacturer, Addwerk is proving a textbook example of how their interface software can accelerate automation processes.
Addwerk is a manufacturer in the most modern of senses, using state of the art 3D printing technology to high quality produce end-use industrial parts. What makes Addwerk such an ideal test case is the company’s approach to automation; their ambitious goal is to have a fully automated factory workshop that can 24/7 without any human intervention.
The key challenge facing Addwerk is their ability to introduce new and highly customised industrial parts into their production lines as quickly as possible.
Lluis Planella Pares, CEO and founder at Addwerk explained:
“The main problem that we have is a lot of orders with different parts – very variable parts – that need to be post processed and delivered at high speed and at a high rate, and we need to sort them as automatically as possible.”
The partnership between the two companies is addressing this challenge head-on, specifically with the sorting processes.
Even with steady growth in industrial robotics usage, typically the automation of sorting with such a high level of variability would involve specialist programming knowledge and the time to reprogramme hardware.
In comparison, Extend Robotics’ solution provides users with full depth perception of 3D environments and accessible controls using intuitive arm-and-hand gestures in an immersive, real-time experience. This enables even non-technical users to execute and automate processes, overcoming the challenge of the levels of variability involved.
As Pares explained further:
“We investigated several ways to be able to sort the orders and the variability of the parts we have, and we arrived at the conclusion that a mix of human intervention and robotisation was the best solution.
“This mix of human intervention and robotised intervention was best solved by Extend Robotics… I think that now we have a solution that helps us a lot with being able to process parts that are massive or delicate without having to rely on a program.”
Speaking about this latest test case, Dr Liu, CEO of Extend Robotics said:
“One of the biggest obstacles to efficient rapid automation is when processes involve a high level of variability.
“Now, thanks to this partnership, there can be no doubt that our tech solutions can overcome this obstacle effectively, efficiently and with a demonstrable level of quality and accuracy.”