Product Focus: Modular Large Robots for High Payload Assembly
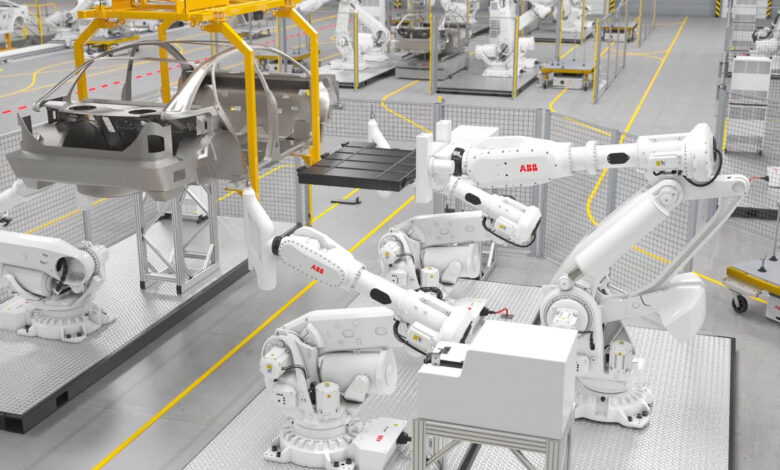
ABB Robotics (Auburn Hills, MI) is continuing the expansion of its modular large robot portfolio with the introduction of the new IRB 7710 and IRB 7720 that made their debut at Automate 2024 this week. These latest robots are ideally suited for use in industries such as automotive, construction, and logistics. They were working in a fully functional automotive production cell at ABB’s booth, performing car body component material handling, spot welding, and arc welding.
The new robots, combined with recently launched IRB 5710-IRB 5720 and IRB 6710-IRB 6740, offer a combined total of 46 different variants capable of handling payloads between 70 kg-620 kg, to give customers a new level of flexibility, greater choice, and performance in their operations.
“As businesses introduce new technologies and components to meet productivity and sustainability goals, we’ve engineered our modular large robot portfolio to enable them to select the best robots and variants to allow them to efficiently undertake their operations” said Marc Segura, President, Robotics Division at ABB. “With the most comprehensive portfolio of mechatronic platforms, industrial robots, cobots, and AMRs in the marketplace, the latest robots extend our portfolio even further, helping our customers navigate labor shortages and ensuring they remain competitive, while operating in a sustainable manner.”
ABB’s new IRB 7710 and IRB 7720 robots offer 16 new variants and are ideally suited to support applications across various industries. Operators can choose from a wide range of ABB robots to ensure they have the ideal variant to handle various applications for electric vehicles (EV), hybrid, and traditional car production — spanning from press automation, body-in-white, EV battery construction, and final assembly. These robots are perfect for high payload assembly, such as giga casting, high speed press tending and palletizing, as well as high accuracy contact applications, such as machining and friction stir welding.
Powered by OmniCoreTM, the new robots achieve class-leading motion control with path accuracy down to 0.6 mm, even with multiple robots running at high speeds of up to 1600 mm/s and moving payloads of up to 620 kg. Customers can also benefit from an up to 25 percent reduction in cycle times [IRB 7710 compared with its predecessor IRB 7600 running in the same payload of 500 kg on the previous controller IRC5] further enhancing productivity and quality.
In the automotive industry, the all-new IRB 7710 with the latest OmniCore controller, will boost the production output of robotic press lines from 12 to 15 strokes per minute to produce 900 parts per hour. Furthermore, in the construction sector, the new robots will support the growth in modular construction, capable of constructing steel building frames and surface finishing, with improvements in speed and quality.
The IRB 7710’s energy efficient design in combination with OmniCore’s re-generation technology achieves up to a 30 percent energy reduction, while the built-in power pack can relay energy back to the grid. Automate Booth #2239
For more information, visit https://new.abb.com/products/robotics/robots/articulated-robots/irb-7710 .