Renault’s digital transformation continues with autonomous picking robots
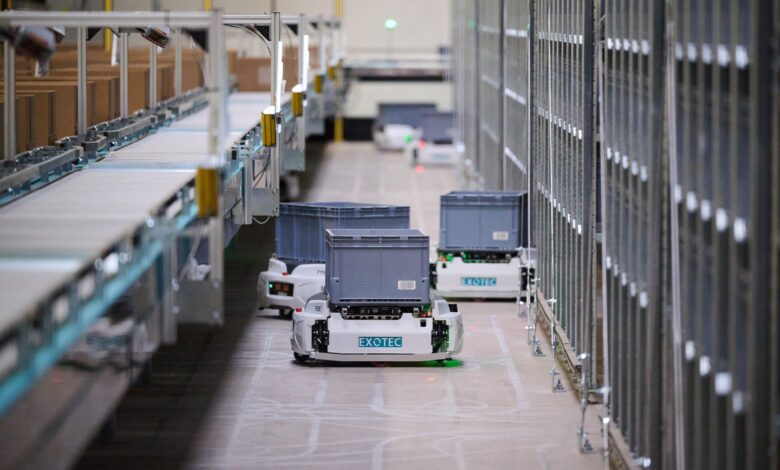
Renault Group x Exotec robots. Image Crochez / Exotec, with permission.
The Renault Group has sought to position itself further at the forefront of innovation in automotive logistics by partnering with the company Exotec. This arrangement is part of the continuing digital transformation journey of the French car group and the arrangement sees an expansion in robotics in the car industry.
Renault Group has selected Exotec to automate the site of the Villeroy Parts and Accessories Logistics Department. This includes the use of 191 Skypod® robots that will automate the flow of parts from receipt to shipment, thus dividing the processing time of customer orders by a factor of six.
Exotec is a French firm that designs “goods-to-person” robotic solutions for the warehouses. The robots can travel at speeds up to 4 metres per second.
Exotec’s robots are autonomous and equipped with advanced navigation and handling capabilities. The robots have a compact design and they have also been designed for considerable agility, allowing them to move quickly and efficiently in complex logistics environments where each robots can move in three dimensions without the need for complicated infrastructure.
Agility is also twinned with safety so that the robots can move around other equipment and workers. In addition, the robots can operate in both chilled and ambient temperature environments.
The main functions of the robots are:
Injection
Here pallets for storage in the facility are automatically injected into 60-litre trays. These are then transported by a robot that places them in the storage racks.
Picking
When customer orders are received, picking tasks are assigned to picking stations. A robot then collects the reference of the items ordered to bring them to the picking stations. This operation is repeated for each item ordered.
Shipping
Once the items are prepared, the packages are transported to the shipping area where they are sealed and routed to the shipping docks to be loaded onto the trucks.
Combined, the preparation time of an order (from the beginning to the delivery of the package to shipments) has been reduced down to 20 minutes. Previously, this operation was carried out in 2 hours.
In addition, this so-called “good to men” solution aims to improve the working conditions of employees.
The move also makes it possible to reduce the Villeroy site’s energy consumption by 30 percent compared to the traditional solution.