Robotics Manufacturing Hub to help small and midsize U.S. manufacturers compete
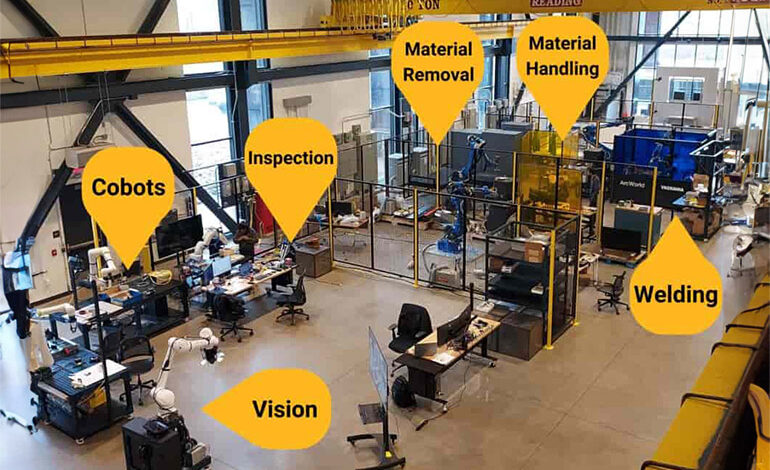
Listen to this article |
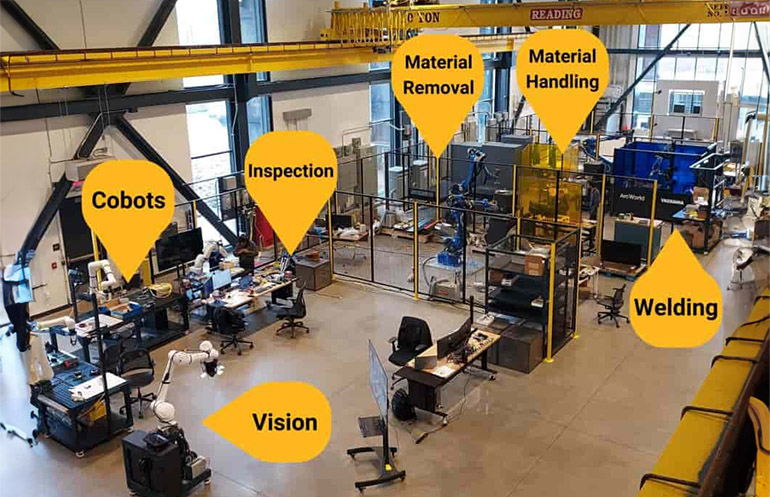
The Robotics Manufacturing Hub is modular, adaptable, and multi-use, with OEM diversity. Source: The ARM Institute
When the ARM Institute launched its Robotics Manufacturing Hub about a year ago, it quickly realized that U.S. manufacturers weren’t looking at robotics and automation because they weren’t interested in the technology. Instead, the barriers to automation loomed so large that it was impossible for small and midsize firms to know where to start.
When the ARM Institute announced its no-cost Robotics Manufacturing Hub for manufacturers in the Pittsburgh region, its pipeline of interested manufacturers rapidly filled. With the ARM Institute offering a pathway to minimize the risks they associate with robotics and automation, U.S. manufacturers were, and still are, eager to explore the possibilities.
Larger manufacturing firms can more easily navigate the process of implementing automation. With greater general resources, in-house R&D, financing to invest in the upfront costs, and more time to explore solutions, they’ve more successfully been able to see the process through from start to finish.
Small and midsize manufacturers (SMMs) have to navigate more risk. They need to spend more time understanding how the changes will affect their operations. They often lack in-house robotics expertise, and they need systems that will dynamically meet their needs without requiring constant upkeep when, in many cases, their workforce is already strained.
The ARM Institute’s Robotics Manufacturing Hub is a free resource to help manufacturers navigate these barriers and others by identifying the best business cases for robotics, testing the systems within the manufacturer’s budget, and offering a path to implementation. Part of this solution includes the ability for SMMs in Southwestern Pennsylvania to work directly with the institute’s team of robotics engineers and get hands-on with advanced technologies in the institute’s Pittsburgh facility.
Submit your presentation idea now.
ARM Institute shares case studies
Since the Robotics Manufacturing Hub’s creation, the ARM Institute has worked with several manufacturers in the Pittsburgh region to explore their challenges and help them understand where robotics can address these challenges.
For example, the ARM Institute worked with a manufacturer of castings and forgings to automate its manual quality-inspection process. Partnering with FARO and NEFF Automation through the Robotics Manufacturing Hub, the ARM Institute performed a proof-of-concept of a Universal Robots cobot controlling a FARO laser scanner. The manufacturer plans to pursue implementation.
The ARM Institute also worked with a company that needed to package heavy iron and steel parts into shipping containers, creating an ergonomically uncomfortable task for a human worker. In this situation, requirements for the robotic end effector were highly specific, and it’s critical to calculate the correct pick place on the parts and speed limitations of the robot to move heavy parts and prevent failure or injury.
The ARM Institute is working with its member CapSen Robotics on a solution.
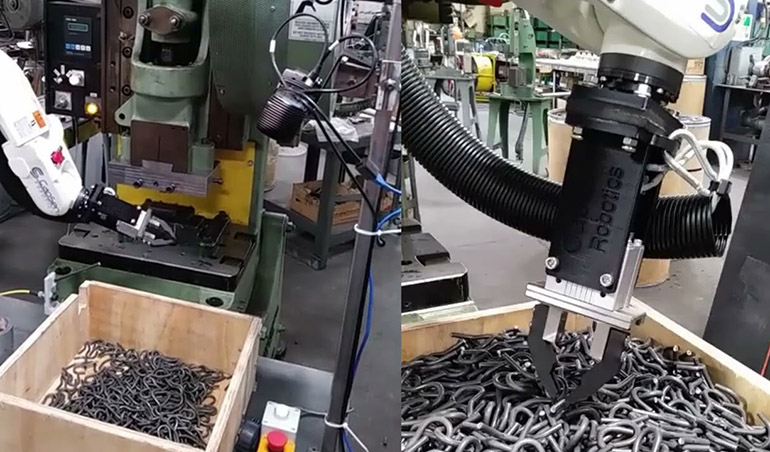
CapSen Robotics has designed end effectors to sort metal parts. Source: CapSen Robotics
Inside the Robotics Manufacturing Hub facility
Much of this work is completed using the ARM Institute’s headquarters as a neutral ground for exploration and prototyping, giving manufacturers access to equipment before they commit to installing any system.
This facility is modular, adaptable, and multi-use, with OEM diversity to directly meet each manufacturer’s individual needs. ARM Institute engineers work directly in the lab and interface between suppliers and manufacturers to act in the SMM’s best interest and ensure that the work will address the specific challenges the company is facing.
Below is a brief overview of the equipment available through the Robotics Manufacturing Hub and application areas that can be addressed using this equipment:
Collaborative robots:
- Universal Robots (UR) 5e
- Yaskawa HC10
- FANUC CRX-10 Ai/L
- FANUC CRX-20 Ai/L
The cobots can be configured for the following applications:
- Small part handling
- Pick and place
- Vision-guided grasping for pick-and-place applications
- Machine tending
- Process tasks including gluing and dispensing
- Inspection with Faro ARM Quantum with Laser line probe and CMM
- Inspection with Cognex 2D imaging
- Inspection with Cognex 3D imaging
Industrial robots
- Epson VT6L
- Yaskawa GP-88
- Yaskawa GP-180
- Yaskawa Weld Cell with positioner
The industrial robots can be configured for the following applications
- Large part handling
- Large part palletizing
- Large part pick and place
- Force controlled grinding and polishing
- Welding
Get involved with the Robotics Manufacturing Hub
Small and midsize manufacturers in the Pittsburgh region can get a free automation assessment and use the Robotics Manufacturing Hub at no cost, thanks to funding from the Southwestern Pennsylvania Region’s Build Back Better Regional Challenge Award. Now is a great time to get started with the hub, as the ARM Institute is looking to work with more manufacturers.
In the future, the ARM Institute hopes to expand these services to manufacturers beyond this region and encourages those with interest in using or housing these services to reach out. In addition, the ARM Institute’s member ecosystem can use the Robotics Manufacturing Hub as a benefit of membership.
According to the ARM Institute’s “Future of Work” study released last week, industry trends include keeping people in the loop and the need for organizations to learn how to use data as artificial intelligence increases in importance. As a result, the institute noted that manufacturers and training centers must develop programs to help workers develop the skills needed to stay competitive and adapt to new technologies.
U.S. manufacturing resiliency is the cornerstone of our national security. The ARM Institute’s Robotics Manufacturing Hub addresses a critical need in helping to provide SMMs with the resources that they need to explore and implement automation, enhancing their competitiveness and benefiting the full manufacturing ecosystem.
About the author
Larry Sweet last year became director of engineering at the Advanced Robotics for Manufacturing (ARM) Institute in Pittsburgh. He has experience in bringing emerging technologies into production by increasing their Technology Readiness Level, concurrent with improvements in factory floor processes and workforce skills.
Sweet was previously the director for worldwide robotics deployment at Amazon Robotics, leading technology transition and system integration for all internally developed automation into Amazon’s global network. He has also held senior manufacturing and technology roles at Symbotic, the Frito-Lay, United Technologies, ABB, FANUC, and GE. Sweet spoke at the 2024 Robotics Summit & Expo in May.
Editor’s note: This article is syndicated from The Robot Report sibling site Engineering.com.