Robots Automate Assembly of Engine Valves
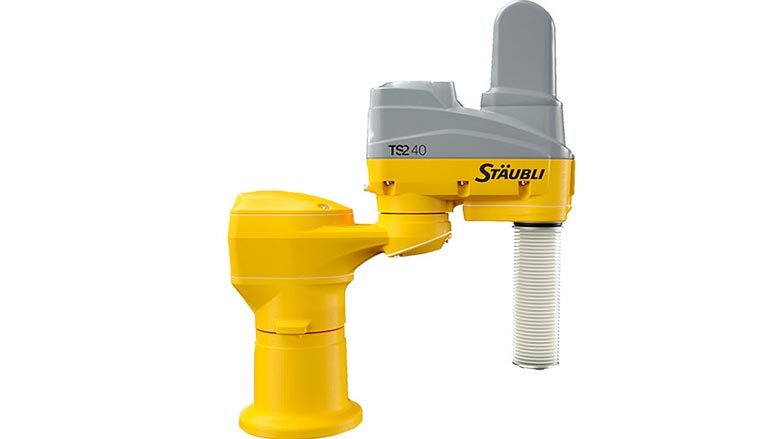
A crankcase ventilation system removes unwanted gases from the crankcase of an internal combustion engine. The system usually consists of a tube, a one-way valve and a vacuum source, such as the inlet manifold.
The unwanted gases, called “blow-by,” are gases from the combustion chamber that have leaked past the piston rings. Early engines released these gases to the atmosphere simply by leaking them through the crankcase seals. Positive crankcase ventilation systems send the crankcase gases back to the combustion chamber, as part of the vehicle emissions control, to reduce air pollution.
Although an engine only needs one pressure relief valve, it is a wear part and must be replaced periodically. As a result, millions of the valves must be assembled annually.
German company ElringKlinger markets a variety of plastic automotive components, such as this pressure relief valve for electric vehicles. Photo courtesy ElringKlinger
One company doing just that is Langer GmbH & Co. Based in Illmensee, a small town in southern Germany near the Switzerland border, Langer was founded in 1975. The company employs 160 people and manufactures injection-molded plastic parts and the molds for making them. It also offers design, assembly and test services to its OEM customers.
One of those customers is global automotive supplier ElringKlinger AG of Dettingen an der Erms, Germany, a manufacturer of pressure relief valves and other parts.
ElringKlinger’s valve consists of two components: an injection-molded plastic part and a membrane made of fluoroelastomer. Assembly of the valves is an intricate process that poses multiple challenges. Tolerances are in the hundredth of a millimeter range, and each valve must pass rigorous quality assurance procedures. Langer assembles some 3 million pressure relief valves annually.
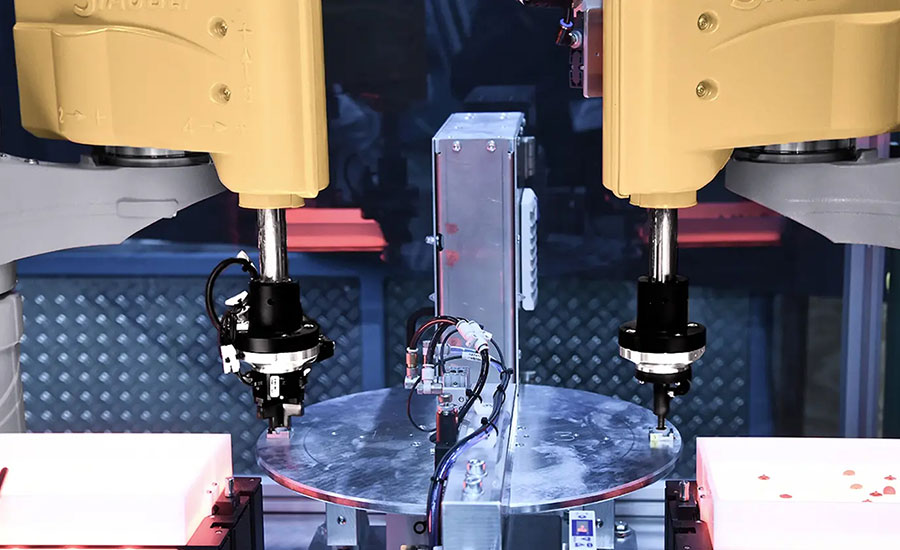
Two high-speed SCARA robots manage all handling and assembly processes in the compact cell. Photo courtesy Stäubli
The components are small and delicate. The fluoroelastomer membranes have a diameter of just 5 millimeters and must be inserted in the injection-molded part within a tolerance of just a few hundredths of a millimeter.
Langer produces the valves on an innovative high-speed assembly system featuring two TS2-40 SCARA robots from Stäubli. The high-precision four-axis machines manage all handling and assembly steps in the cell, which is based on a rotary indexing table.
The process begins with the delivery of the two components—the injection-molded casing and the membrane—which are delivered via two feeder systems. A stationary image processing system located above the feed tray supplies positional data to the first of the two SCARA robots, enabling it to pick up an injection-molded part and correctly position it in a fixture on the indexing table.
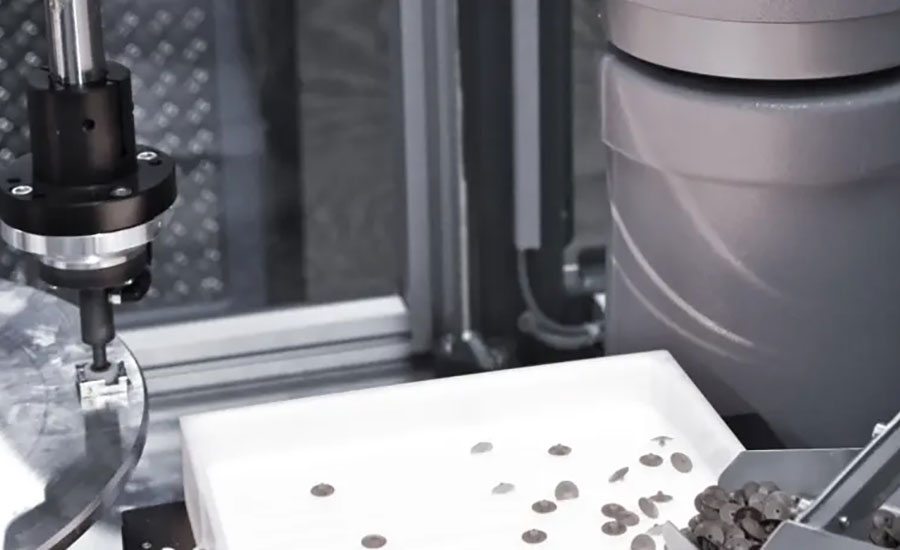
A SCARA robot retrieves a membrane from the feeder system and inserts it into the part. Photo courtesy Stäubli
The table then rotates to the first of the two quality assurance stations. Here, an image processing system checks that the part conforms to size and has been correctly deburred.
The membrane is attached at Station 3, which is quite a difficult process. The second SCARA fetches a membrane from the feeder system and inserts it into the part. The robot must operate with dynamics and precision while fulfilling rigorous cycle time criteria.
Once these stages have been completed, the valve passes through another quality assurance station, where a vacuum and overpressure test takes place. The rotary table then returns the part to the station where its journey began. The infeed robot also handles the removal of the finished and tested parts.
Langer engineers particularly appreciate the assembly system’s “outstanding” autonomy. The machine requires just one manual provisioning of parts per shift.
The system assembles the valve with a defect rate of just a few parts per million.
In addition to its high output and availability rate, Langer engineers particularly appreciate the assembly system’s “outstanding” autonomy. The machine requires just one manual provisioning of parts per shift. The cell operates with hardly any interruption.
“The outstanding performance of the Stäubli TS2-40 makes a decisive contribution to the success of the entire assembly cell,” says Markus Beierl, head of injection molding at Langer.
The TS2-40 has a maximum reach of 460 millimeters and can carry a maximum payload of 8.4 kilograms. Positional repeatability is ±0.01 millimeter. The Z axis stroke is 200 millimeters. (A Z axis stroke of 400 millimeters is available as an option.)
ASSEMBLY ONLINE
For more information on robotic assembly, visit www.assemblymag.com to read these articles:
Robot Automates Handling of Silicon Wafers
Robots Assemble Pressure Sensors
A Roundup of New Robots