The Interplay Between Robotics and Artificial Intelligence in Manufacturing
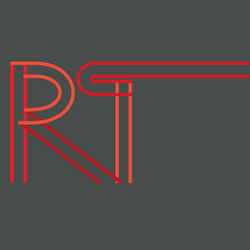
The growth opportunities for AI and robotics in manufacturing are vast and projected to reach $182 billion globally by 2027. Companies that fail to adopt these exponentially advancing technologies as part of their process risk falling behind, as smart factories powered by intelligent machines become the norm.
How Artificial Intelligence is used in Robotics
Artificial intelligence (AI) and robotics are revolutionizing manufacturing, providing scale, speed, and time-to-market advantages. According to the World Economic Forum, over 50% of manufacturers will adopt AI by 2025 as these technologies are proving effective in boosting shop floor efficiency, quality, and flexibility.
AI gives robotics programming and manufacturing platforms unprecedented adaptability, scale and speed. AI and robotics also are the catalysts that enable manufacturers to achieve more in less time and at a lower cost. Automating repetitive, dangerous, or ergonomically taxing manual tasks, including heavy lifting, materials handling, and assembly is just the start of these two technologies’ many contributions to manufacturing.
Combining artificial intelligence and robotics across shop floors also automates quality inspection, where AI helps reduce defects and scrap. The growth opportunities for AI and robotics in manufacturing are vast and projected to reach $182 billion globally by 2027. Companies that fail to adopt these exponentially advancing technologies as part of their process risk falling behind, as smart factories powered by intelligent machines become the norm.
Integrating robotics and AI is paying off in manufacturing
Integrating Artificial Intelligence and robotics continues to revolutionize manufacturing by providing new automated methods to improve production efficiency and quality while reducing costs. Powered by the data AI and machine learning algorithms produce, robots can now perform complex manual tasks with unmatched precision and speed. This automation provides the accuracy, scale, and speed manufacturers need to stay competitive, meet customer delivery dates, and stay competitive during turbulent economic times. Key applications yielding major benefits include:
Automating manually repetitive, dangerous tasks
Robotic arms with sensors, computer vision, and artificial intelligence can take over heavy lifting, materials handling, assembly, and other repetitive manual work. DELMIA Robotics solutions provides the programming and simulation tools to enable this automation with material-handling robots. This frees the human workforce for higher-value functions and improves safety by reducing ergonomic strains. According to McKinsey, automating predictable physical work could boost global productivity by 0.8 to 1.4% annually.
Enabling mass customization and design-to-manufacturing
Orchestrating AI and robotics in combination with manufacturing execution systems (MES) and enterprise resource planning (ERP) systems is defining the future of mass customization and design-for-manufacturing. These technologies enable manufacturers to produce customized products at scale profitably. AI automates repetitive design and production tasks, freeing engineers to focus on delivering faster innovation. DELMIA optimizes robotic routings, work instructions for each unique configuration, and is integral to ensuring mass customization and design-for-manufacturing strategies succeed.
Robotics manufacturing flexibly switches between real-time product variations while ensuring accuracy and precision. AI optimizes production plans and logistics in real time, tailoring them for mass customization. Intelligent design tools use AI to optimize manufacturability. Together, AI and robotics amplify the advantages of integrated design-to-manufacturing platforms, accelerating throughput, quality, and profitability. Manufacturers can now deliver large-scale, small-batch tailored products and capture more revenue opportunities.
Optimizing production planning
DELMIA Robotics optimization leverages AI algorithms to analyze terabytes of manufacturing data, identifying patterns and anomalies for optimizing planning and scheduling in real time. AI-based DELMIA techniques effectively detect and predict potential production constraints and simulate scenarios to minimize downtime and bottlenecks.
Combining DELMIA Robotics’ AI-based manufacturing intelligence, robotics simulation, and integration with manufacturing execution systems (MES) and enterprise resource planning (ERP) further improves production yield rates and quality consistency across all production centers. When the insights from DELMIA’s unified robotics, MES, and ERP data become ingrained, it leads to greater customer satisfaction, repeat sales, and profitability.
Increasing predictive maintenance accuracy
Combining IoT, IIoT, and Programmable Logic Controller (PLC) sensors and AI predictive analytics minimizes unplanned downtime of machinery, including robotics across shop floors. Algorithms detect early performance anomalies and predict maintenance needs before failures occur. Instead of rigid schedules, maintenance is performed only when required. According to PwC, AI-enabled predictive maintenance can reduce maintenance costs by 10-40% and decrease overall downtime by 20-50%. In one case, AI helped a rail company cut unplanned downtime by 35%, saving an estimated $50 million. As these examples highlight, predictive maintenance powered by AI delivers major efficiency and cost gains.
DELMIA robotics also helps validate production systems and robot programming within a 3D collaborative environment before building the production system using Virtual Twin techniques and technologies. It can also enable the virtual commissioning of robotics systems to confirm that they work as expected before the control program is downloaded to actual equipment. This can further reduce the risk of failures and optimize the performance of robotics systems. DELMIA robotics is a valuable tool for enhancing predictive maintenance with artificial intelligence in manufacturing.
Improving quality control
Robots with computer vision and AI-based deep learning can inspect products for defects autonomously before they leave production centers, reducing the need for return material authorizations (RMAs) to customers. This lowers customer complaints and boosts customer loyalty and trust by catching defective products before shipment. AI-based algorithms learn from the data they capture, analyze, and act on, strengthening the quality muscle memory of production centers using these technologies. McKinsey found that advanced image recognition techniques for visual inspection and fault detection with AI can increase productivity by up to 50%. McKinsey also found that AI-based visual inspection with image recognition can improve defect detection rates by up to 90% compared to human inspection. Moreover, DELMIA Robotics software can help validate and optimize robot programming and simulation in a Virtual Twin 3D collaborative environment before building the production system. This can further enhance the performance and reliability of robots for quality inspection.
How DELMIA Robotics is defining the future of manufacturing
Manufacturing is transforming with AI and robotics, which offer scale, speed, and time-to-market advantages. The AI in manufacturing market size will grow from $2.3 billion in 2022 to $23.6 billion by 2030, with a 31.1% CAGR. The industrial robotics market will reach $86.6 billion by 2027, up from $50.3 billion in 2021. These numbers show how AI and robotics play a vital role in manufacturing.
AI and robotics power design-to-manufacturing platforms that optimize complex tasks, increase quality and productivity and streamline customized product development. Intelligent robots work with human workers, improving flexibility, precision, and safety. AI and robotics enable a company with agile manufacturing, which allows mass personalization and on-demand production, meeting customer demand and supply chain dynamics.
AI and robotics make the factories of the future smarter and more efficient. Manufacturers need to use these exponential technologies to gain a competitive advantage. DELMIA Robotics software helps manufacturers validate and optimize robot programming and simulation in a 3D collaborative environment before building the production system. This reduces the risk of failures, saves time and cost, and improves the performance and reliability of robots for various production processes.
Louis Columbus, is senior industry marketing manager at DELMIA. DELMIA empowers manufacturing, supply chain and service providers to efficiently plan, manage, optimize and execute their operations.